Es geht wieder zurück nach Blomberg, an den Hauptstandort von Phoenix Contact. Hier residiert auch eine Tochter des Unternehmens. Eine besonders attraktive zudem. Sie wird Protiq genannt und von Dr. Gärtner geleitet.
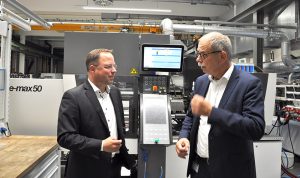
„Der Kunde schickt den Zwilling, und wir drucken daraus das reale Ebenbild.“ Was sich komplex anhört, ist heutzutage Alltag, der 3D-Druck ist aus dem industriellen Umfeld nicht mehr wegzudenken. Bei Phoenix Contact hat er einen Namen: Protiq. Die Tochtergesellschaft wird von Dr. Ralf Gärtner geleitet. Und der schränkt, man ahnt es, ein: „Digitaler Zwilling ist bei uns zu hoch gegriffen. Wir arbeiten mit 3D-Datensätzen, die lediglich mit wenigen Informationen angereichert werden.“
Um zu drucken, müssen die Daten, genauer der Digitale Zwilling, direkt vorliegen. Die werden in der Regel als CAD-Datensatz vom Auftraggeber angeliefert. Die typische Anreicherung eines bestehenden realen Produkts mit zusätzlichen Daten, also die Komplettierung mit zusätzlichen Produktinformationen bis hin zu Rechnungs- und Versandinformationen, wird bei Protiq auf den Kopf gestellt.
„Wir starten mit den digitalen Daten, und dann erst erzeugen wir mit der additiven Fertigung das reale Produkt. Das durchläuft dann alle unsere Systeme, bis hin zu Warenwirtschaft, zum Versand und zum Kunden“, führt Dr. Gärtner aus. Und was ist, wenn es keine CAD-Daten gibt? „Dann scannen wir, z. B. mithilfe von Computertomographen. Das ähnelt vom Prinzip her dem typischen 2D-Druck, wo man auch zunächst tippen muss, bevor gedruckt werden kann.“
Nur digital geht es nicht
Hat ein Konstrukteur ein CAD-Modell fertig designt, kann ein Drucker dieses über Nacht in die Realität bringen. Dann kann bereits nach wenigen Stunden am realen Produkt getestet werden. „Das beschleunigt die Produktentwicklung enorm“, erklärt Dr. Gärtner.
Zunächst gänzlich digital erfolgt dagegen die Topologieoptimierung. Mit diesem Verfahren wird einem 3D-Modell eine optimierte Form gegeben, die den Spagat zwischen Gewichtsreduzierung und Steifigkeitsoptimierung und Stabilität auf oft verblüffende Weise erzielt. „Das ist aber nur ein Arbeiten am CAD-Modell, das nicht das Ziel hat, einen Digitalen Zwilling zu erzeugen“, schränkt Dr. Gärtner ein. „Wir machen nur den Datensatz besser, um ihn dann auszudrucken.“
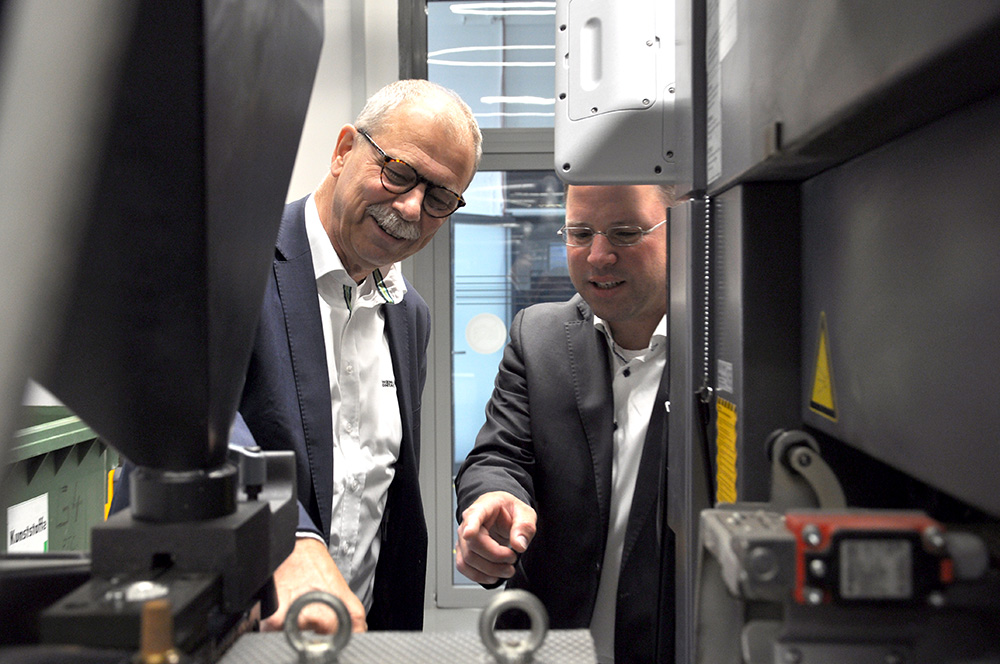
Wie selbstverständlich zwischen den digitalen und realen Welten hin- und hergesprungen wird, verdeutlicht folgender Vorgang: In einem Druckvorgang können hunderte Kundenaufträge gleichzeitig bearbeitet werden. All diese Teile müssen im Nachgang identifiziert und dem jeweiligen Kundenauftrag händisch zugeordnet werden. „Die totale Verschwendung der Arbeitskraft eines menschlichen Wesens“, so Dr. Gärtner. Diese Zuordnung ist der Fluch des Batch-Prozesses, der Bündelung diverser Druckaufträge zur optimalen Anordnung im Druckerbauraum. Der Prozess ist nötig, um die Kapazitäten des 3D-Druckers optimal zu nutzen.
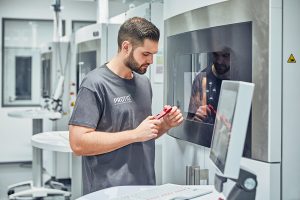
Produktion mithilfe von Zwilling und KI
„Was wir ganz aktuell geschafft haben, ist die Identifizierung dieser 3D-gedruckten Teile und die Zuordnung zu Kundenaufträgen zu automatisieren. Das geschieht, indem ein Kamerasystem die Vielzahl der Teile aufnimmt und mithilfe von lernender künstlicher Intelligenz dann die Teile identifiziert, die zu einem Kundenauftrag gehören. So findet ein Abgleich statt zwischen realen Gegenständen und dem digitalen Ebenbild, das den Herstellungsprozess durchlaufend begleitet.“
Noch vor kurzem Science Fiction, heute schon Realität: „Durch unsere Druckkapazitäten in den USA und Indien sind wir in der Lage, den Digitalen Zwilling sozusagen vorauszuschicken und sein reales Ebenbild vor Ort drucken zu lassen. Das spart enorm Zeit und Logistikkosten.“
Wir füttern ihn
Wir trainieren ihn
Wir steuern mit ihm
Wir drucken mit ihm
Wir haben ihn!