It is back to Blomberg, the main location of Phoenix Contact. A subsidiary of the company also resides here. A particularly attractive one at that. It is called Protiq and is managed by Dr. Gärtner.
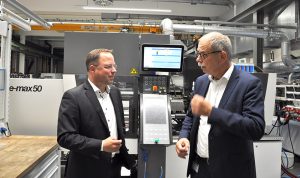
“The customer sends the twin, and we use it to print the real image.” A complex-sounding concept has now become the ordinary – 3D printing has become an indispensable part of the industrial environment. At Phoenix Contact, it has a name: PROTIQ. The subsidiary is managed by Dr. Ralf Gärtner. And, as we have come to expect, he downplays the idea. “The digital twin is way too exaggerated here. We work with 3D datasets that are simply enriched with small amounts of information.”
In order to print something, the data, or more precisely the digital twin, needs to be available directly. The customer usually supplies it directly as a CAD dataset. Protiq turns the conventional enrichment of an existing real product with additional data, i.e. the completion with additional product information up to billing and shipping information, on its head.
“We start with the digital data, and only then do we produce the real product with additive manufacturing. This then runs through all of our systems, right through to merchandise management, dispatch, and to the customer,” explains Dr. Gärtner. And what if there is no CAD data? “Then we scan, using computer tomography for example. The principle is similar to typical 2D printing, where you have to type before you can print.”
It doesn’t work with just digital
Once a designer has finished designing a CAD model, a printer can make it real overnight. After just a few hours, the real product is available for testing. “This accelerates product development enormously,” explains Dr. Gärtner. Topology optimization, on the other hand, is initially done entirely digitally. This method is used to give a 3D model an optimized shape, one that achieves the balancing act between weight reduction and stiffness optimization and stability in often astonishing ways. “But this is just work on the CAD model, which does not have the goal of creating a digital twin,” Dr. Gärtner qualifies. “We are just improving the dataset so that we can print it out.”
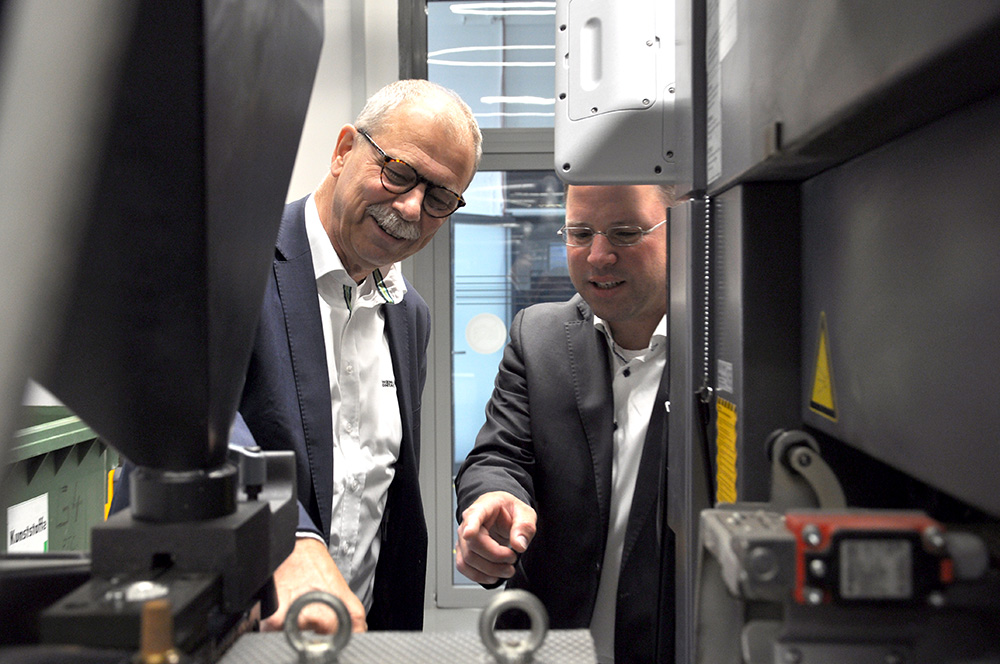
Just how naturally we jump back and forth between the digital and real worlds is illustrated by the following process: Hundreds of customer orders can be processed simultaneously in one printing process. All of these parts then have to be identified and manually assigned to the respective customer order. “This is a complete waste of the effort for a human being,” says Dr. Gärtner. This assignment is the curse of the batch process, bundling various print jobs for optimum arrangement in the print room. The process is necessary to make the most of the capacity of the 3D printer.
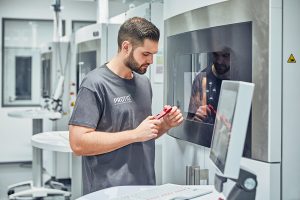
Production using twin and AI
“Only very recently have we managed to automate identifying these 3D-printed parts and assigning them to customer orders. This is done by using a camera system to record the large number of parts and then using learning artificial intelligence to identify the parts that belong to a customer order. Here, a comparison is made between real objects and the digital image that accompanies the manufacturing process.”
What seemed to be science fiction just a short time ago is now reality. “Thanks to our printing capacities in the USA and India, we are in a position to send the digital twin ahead, so to speak, and have its real image printed on location. This saves a lot of time and logistics costs.”
We feed it
We train it
We control with it
We print with it
We’ve got it!