It goes back to Bad Pyrmont. There you will find a particularly hot trace of the digital twin – namely in the printed circuit board production, which is at home here.
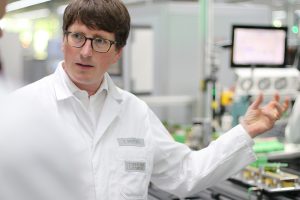
The digital companion has very tangible effects when it arrives in production. This is because in the Inline production line for PCBs, the production process is not controlled by a central control center. Instead, it’s controlled by the twin. And it does so by steering the stroller to stay in the picture. The DNA in the twin contains all the information on the production steps and their sequence.
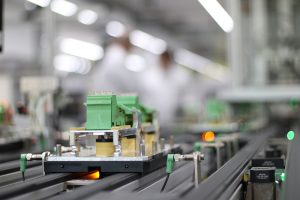
Dr. Till Potente is Head of Production, and he explains to us what this shift in intelligence involves. “The data that each individual product already has is loaded onto an RFID chip that is on board a transportation vehicle, the carrier. This carrier then travels on a conveyor belt from station to station. This transporter “knows” where it has to go thanks to the information on the chip. If, for example, its cargo needs a marking, the carrier switches the downstream points so that it moves onto the section of line leading to the laser.
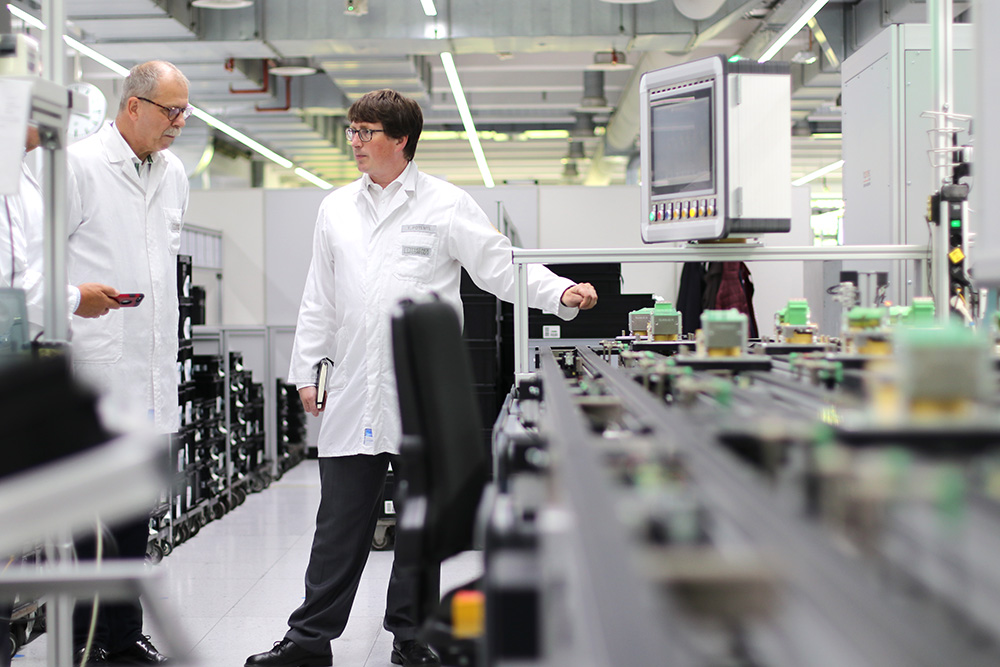
It therefore autonomously controls precisely which work steps it has to go through until the product, in this case the real twin, has reached completion. Finally, it then goes to quality control, where the properties are tested against the DNA.”
The component is the captain
But what’s the advantage? “The product controls itself. This allows us to achieve individualizations in production – in other words, to add properties and components to an order – at lightning speed. This ensures maximum flexibility in our production line.” Thanks to the data from the digital twin and coordinated machine technology, industrial batch size 1 production, as it were, can be realized. “Of course, not in real mass production, where we would have to rely on a central control center again,” Dr. Potente is quick to point out, “but with small-volume orders with great variability, the advantage of digitalization comes into its own here.”
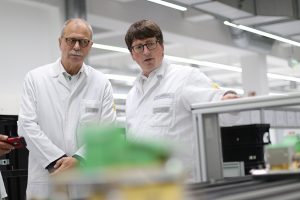
He adds, “By the way, this also makes the system itself extremely modular, because we can exchange or add different workstations as needed without restricting ongoing operation. This allows us to react quickly to new requirements or minor disruptions. This makes the process much more stable.” The product controls the system. Or, to be more precise, its digital twin, which is already complete and knows what its real counterpart ought to look like later, does.
We feed it
We train it
We control with it
We print with it
We’ve got it!