Electromobility will experience a huge rise in the coming years. It will not only change the daily street scene, but also the accustomed balance of power in industry, especially among the heavyweights in the sector.
Phoenix Contacts, the successful e-mobility subsidiary of Phoenix Contact, is meeting these challenges not only with ever new technologies and innovations. But also with an expansion in terms of production and logistics. The new plant in the Polish science and technology park Rzeszów-Dworzysko is scheduled for completion by the turn of the year 2020/2021.
What does this mean for the company, for the industry and which topics will determine the discussion in the coming years? An interview with the two Managing Directors of Phoenix Contact E-Mobility, Michael Heinemann and Ralf Döhre, as well as the Managing Director of the new Polish plant, Marwin Achenbach.
Michael Heinemann Marwin Achenbach Ralf Döhre
UPDATE: Mr. Heinemann, Mr. Döhre, Mr. Achenbach, what is the motivation for Phoenix Contact E-Mobility in Poland? What are we planning to do there, and why are we pursuing it?
Heinemann: We are in a very dynamic market with our business unit. We have growth rates in the upper two-digit range. We can no longer handle the volume we have to produce in our traditional plant in Schieder alone. We therefore urgently need to expand our production facilities, even if this means spreading them over several locations. We have therefore decided to build a new plant in Poland to meet this challenge.
UPDATE: And what are your duties there, Mr Achenbach?
Achenbach: Right now I have two functions: One is I am the managing director of the new Polish company we are establishing have. In addition, since February 2020 I have been taking on the main task of commercial management of E-Mobility GmbH here in Schieder. At Phoenix Contact I am since 2006 and was last commercial manager of Power Supplies GmbH in Paderborn. Our own company in Poland underlines the seriousness and effort with which we want to meet our enormous growth.
Döhre: The location is not around the corner. The main focus of the new location is on production. Mainly low-automated products are manufactured there, i.e. high production shares with a lot of manpower. A large part of our product range is currently affected by this; not everything can be automated. And we are experiencing dramatic increases in the number of units.
Here in Schieder, we can’t get this down from the surface area alone, although we are constantly expanding here. In Poland we have now bought a plot of land and are having a building erected for us there, which we then rent. The location and the region offers enough qualified workers for our labour-intensive products, and the land sufficient area for possible future expansion.
UPDATE: What is the scope of the new project in Poland? What size are we talking about?
Döhre: We are building 14,000 square metres for production and logistics, that is two football pitches. In addition, we are building another 1,000 square meters for offices and social rooms.
UPDATE: How many employees are going to work at the new location?
Achenbach: Until 2023 we need a staff of more than 250 employees. We will start with almost 70 employees. We will build up our own management team, and the first new colleagues have already been hired, including a plant manager. And we also have our own HR department in Rzeszów, whose task will be to recruit employees. Industrial engineering and quality control will be added to this, so our team on site will then be well structured.
UPDATE: Where exactly is the new site located? One of the focal points of automotive production in Poland is currently in Poznan, about a three-hour drive from Berlin.
Döhre: Poznan would only be halfway through. The new location in Rzeszów is then another 6 hours’ drive away. It is located about 100 kilometres from the Ukrainian border. Rzeszów is a dynamic, up-and-coming city with universities and many established industrial companies. The region is also called Aviation Valley, as many aviation companies are located in this area.
UPDATE: How are the tasks distributed between the new location and production here in Schieder, Germany? Is there a plan to manufacture only in Poland in the future?
Heinemann: No, not at all. We will continue to have our headquarters here in Schieder. This is where we are close to development, close to all other processes of product creation. We have come to appreciate the short distances between development and production, and we don’t want to lose that. For us, this is an essential part of our self-image.
Döhre: We are currently experiencing the importance of this idea of a headquarter through a major order from an automobile manufacturer. The machines required for this, the processes, the start of production – it takes months of manpower. Many of our industrial engineering experts are busy every day with the skilled workers, project management and quality management to get these foundations up and running. Such a task is impossible at any other location than here, in our headquarters. The more complex a product is and the greater the degree of automation in production is needed, the most effective way is to manufacture the product here in Germany. This is the only way to react quickly to changes in process or technology.
The plant we are now building produces a vehicle charging inlet every 30 seconds. From an economic point of view, such a machine can also be very well located in Germany. We will experience this even more soon. We are vigorously pushing ahead with this automation, even for products that are currently still manufactured manually. This also makes sense for logistical reasons, because our major customers from the automotive industry are mainly located in Germany.
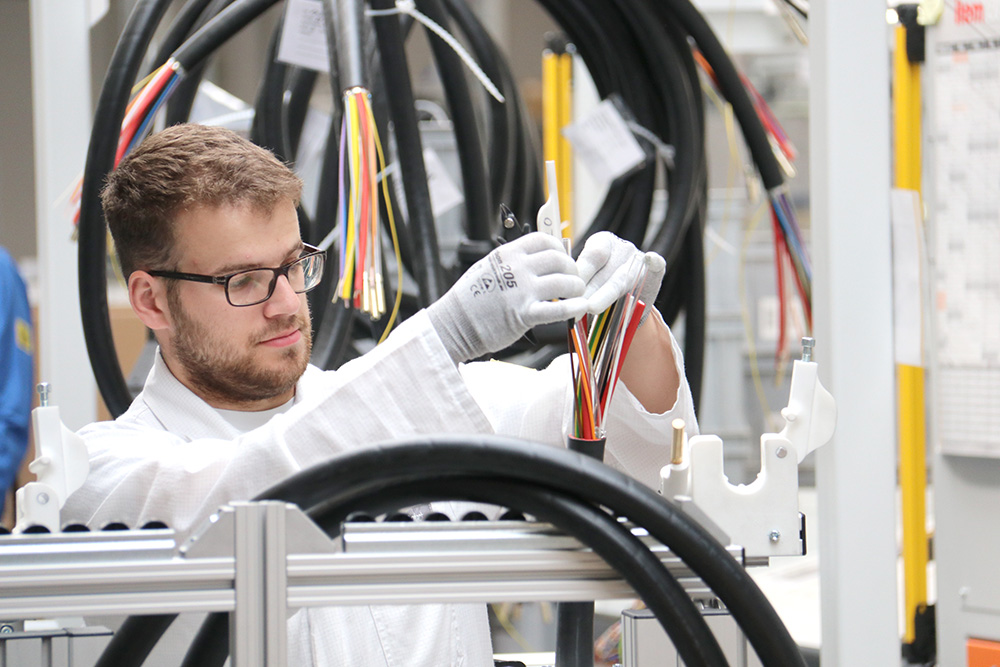
Products that have to experience a great deal of added value, that are offered in great variety, that have heavy cables attached to them, for example, that cannot be automated or that do not have such high volumes – these are also the products that have to be manufactured by hand. This production will take place in Poland.
UPDATE: So, the HPC charging connector, our technological milestone, will also be manufactured in Poland?
Döhre: That would be conceivable. The production of liquid-cooled HPC connectors is extremely demanding. We have very long training periods for employees and need a high level of competence – so a decision will have to be made individually.
UPDATE: With which products will we certainly start in Poland?
Döhre: With what is already being manufactured today at Phoenix Contact Wielkopolska in Nowy Tomyśl. In other words, primarily the AC charging cables and the uncooled DC charging cables. This relocation is taking place first. Initially, this has no influence at all on Germany. Only with an increase in volumes will a change towards automation become noticeable here. Then the Polish production will also take over orders that have been processed here in Schieder until now.
UPDATE: Has Phoenix Contact Wielkopolska already supported in production?
Döhre:When we look at the topic of production, the colleagues in Nowy Tomyśl have done a great job for us in the last 18 months. They have created space, made employees available, including managers. This has enabled us to quickly build up our capacities in Nowy Tomyśl. At the same time, we have also grown enormously here in Schieder, Germany, and moved into a further 5000 m² of space in May. Both in our production in Schieder and at our sister company in Poland: Everyone is working hard – it’s great to see.
Just at the beginning of the year, a large order from the automotive industry, which was already being processed, was suddenly tripled. We had to react quickly and within a few days we have engaged several new employees. The colleagues in Schieder and Nowy Tomyśl have really mastered this brilliantly. In the future, however, we need a plant that is certified in accordance with the IATF 16949 automotive standard and which will allow us to achieve enormous growth in the short term.
Achenbach: However, there will still be general administration functions in Nowy Tomyśl, which we are not building up in parallel: Finance, accounting, HR management – these will continue to be handled by the established structures in Nowy Tomyśl, in close teamwork with the new plant in Rzeszów.
UPDATE: Which customers and markets will be covered by the new plant in the future?
Döhre: Together with the plant in Schieder, the new plant essentially serves the European market with all its charging infrastructure and automotive manufacturers. For the Asian market, we already have a site in China, in Nanjing. It operates “local for local”, which means it concentrates on the requirements there. Poland will be the location for the European mass market, while the technological heart beats here in Schieder. The American market will be served both from Poland and from China.
UPDATE: Are there any long-term plans for additional locations or plants abroad?
Döhre: So far, we have almost 6,500 square meters of production space and warehouse at the German location. In Poland, with the 15,000 square meters, we are already planning to have enough space for growth. In addition, we still have large areas for expansion there, which are in reserve. We can add another 12,000 square meters there. So, for now, our planning is complete.
Heinemann: We will soon be working to full capacity here in Schieder. But if our forecasts come true, Poland will also be fully utilized over a longer period. But with the reserve, we are future-proof.
In the second part of the interview:
The future is called Megawatt connector
Phoenix Contact E-Mobility
Phoenix Contact E-Mobility auf Facebook