Patrick Hartmann weiß genau, wann es zu heiß wird. Denn der Experte für Thermosimulation kann mit Hilfe seines Simulationstools in Gehäusen leistungshungrige Wärmentwickler aufspüren, bevor denen die Puste ausgeht und sie das Zeitliche segnen.
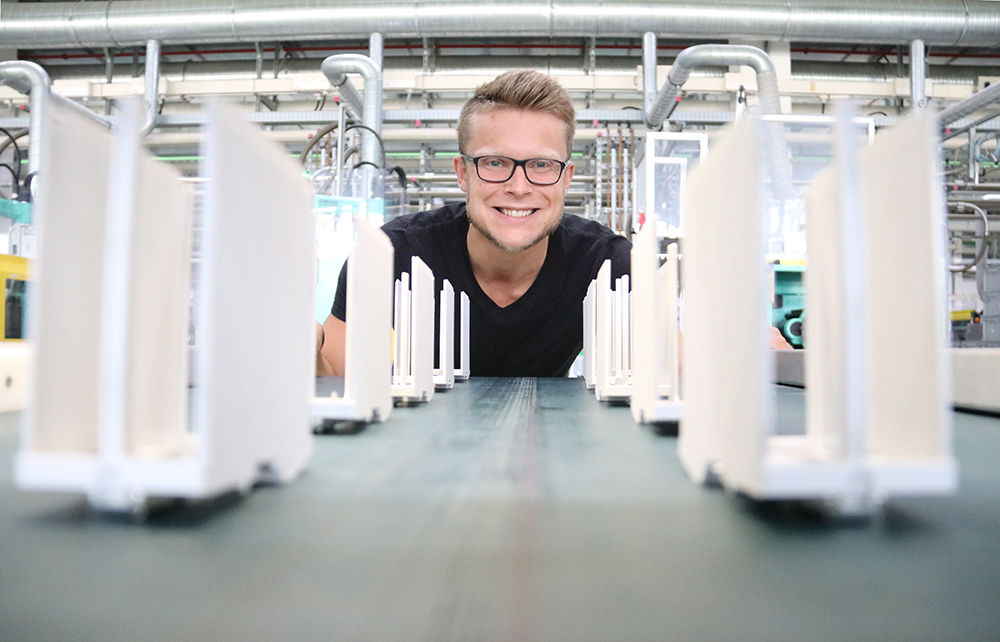
Wärme wird ein zunehmend wichtigerer Faktor bei der Entwicklung von elektrischen Geräten. Immer mehr Leistung soll in immer kleineren Gehäusen Platz finden und dabei noch zuverlässig über Jahre funktionieren. Klimaforschung im Detail – Patrick Hartmann ist Mitarbeiter einer Abteilung, die für die Entwicklung und Produktion von Kunststoffgehäusen zuständig ist.
Elektronik im engen Korsett
„Kunststoff hat als Gehäuse einfach enorm viele Vorteile“, führt der 29-jährige Ingenieur aus. „Es ist leicht, isoliert, ist einfach zu bearbeiten und bietet viel mehr gestalterische Freiheiten als Metall.“ Kein Wunder, dass die Gehäusefertigung bei Phoenix Contact eine lange Tradition hat.
Doch Kunststoff hat zwei gravierende Nachteile. Es leitet Wärme nur sehr schlecht ab und ist hitzeempfindlich. Na und, mag sich der technisch Unbedarfte fragen. Ist doch egal, denn im Inneren der Gehäuse stecken doch nur elektronische Bauteile. „Die sind aber auch hitzeempfindlich“, erklärt der sympathische Experte geduldig. „Kondensatoren können austrocknen, CPUs überhitzen, die Bauteile an Lebensdauer verlieren oder ganze Anlagen und Fertigungsstraßen ihren Betrieb einstellen. Im schlimmsten Falle drohen offene Feuer. Man denke nur an bestimmte Baureihen eines koreanischen Handyherstellers, für die es sogar Flugverbote gab.“
Von welchen Temperaturen reden wir denn eigentlich? „Während in einem normalen Schaltschrank schnell mal 60 °C erreicht werden können, liegen die Temperaturen in Gehäusen deutlich höher. Hier sind 85 bis 90 °C keine Seltenheit.“
Hitze wegrechnen
Patrick Hartmann weiß genau, wovon er spricht. Er beschäftigte sich schon in seiner Masterarbeit als Dualer Student mit dem Thermomanagement in Kunststoffgehäusen. „In immer kleineren Gehäusen werden immer leistungsfähigere Prozessoren und Bauteile eingebaut. Dieser Trend hält ungebrochen an, wird sogar im Zeichen von 5G und Embedded Systems über alle Bereiche der Industrie und Elektronik noch wachsen.“
Im großen Schaltschrank ist das Thema Hitze noch relativ einfach zu lösen. „Man montiert einfach alle Bauteile, die eine hohe Wärmeabgabe haben, nach oben. Im Zweifel baut man noch eine Lüftung ein, die die Hitze absaugt.“ Problem im Gehäusebau: Der Platz ist viel geringer, ergo die Leistungsdichte höher. Und der Kostendruck deutlich größer. Also gilt es, sich im engen Kunststoffmantel anders gegen aufwallende Hitze zu verteidigen. „Hier muss man genau wissen, wo Hitze entsteht. Und dann entweder Lüftungsschlitze einplanen, Bauteile anders positionieren oder Kühlkörper einsetzen, die die Wärme abführen.“
Womit wir bei der Spezialdisziplin des Blombergers sind – der Thermosimulation. „Meist haben Entwickler ein Gehäuse ausgewählt, ihre Komponenten verbaut, alle Anschlüsse realisiert und erst in der Testphase gemerkt, dass das Gehäuse zu heiß wurde. Dann muss aufwändig und mit ziemlich grober Thermografie gemessen werden, um die Hotspots zu identifizieren. Dann wird das Gehäuse modifiziert und erneut getestet. Das ist aufwändig und teuer.
Kühlen Kopf bewahren
Wir haben eine Möglichkeit entwickelt, mit standardisierten Bauteilen und Werten die Entstehung von Wärmequellen schon im Engineering zu simulieren. Unsere Kunden geben an, welches Gehäuse sie gewählt haben, in welcher Umgebung es eingesetzt wird und welche Komponenten im Gehäuse zum Einsatz kommen. Die ordnen wir in der Simulation passend an. Wenn nötig, raten wir zur Gehäusemodifikation, etwa mit Lüftungsschlitzen, oder wir empfehlen den Einsatz eines Kühlkörpers.“ Hartmann fügt hinzu: „Mittlerweile sind wir soweit, dass wir mit der Simulation den Laborversuch quasi ersetzen können.“
Die Experten sind noch einen Schritt weiter gegangen: „Eine solche thermische Simulation kann der Kunde auch für unser neues Gehäusesystem ICS selbst online initialisieren. Zunächst konfiguriert er das Gehäuse nach seinen Anforderungen und definiert anschließend seine thermischen Rahmenbedingungen inklusive Wärmequellen selbst. Die Simulation läuft dann bei uns automatisch ab, wird über ein standardisiertes Verfahren ausgewertet und dem Kunden mittels eines Ergebnisberichtes per Mail zu Verfügung gestellt. Damit erhoffen wir uns viele neugierige Nutzer, die ihre ersten thermischen Untersuchungen auch virtuell selbst durchführen können.“
Das Thema besitzt großes Potenzial. Dermaßen entwickeltes Gehäuse bewehren sich bereits in der Praxis: „Einer unserer Kunden hat ein Gehäuse für ein Multi Channel Monitoring System benötigt. Mit diesem Gerät werden große Wälzlager, etwa in Windturbinen oder Schiffsantrieben, überwacht. Hier haben wir nicht nur die Thermosimulation des passenden Gehäuses durchgeführt und so die optimale Anordnung von Bauteilen und Anschlusstechnik festgelegt, sondern gleich auch noch den passenden Kühlkörper entwickelt, um in den rauen Bedingungen vor Ort für einen zuverlässigen Betrieb der Komponenten zu sorgen.“
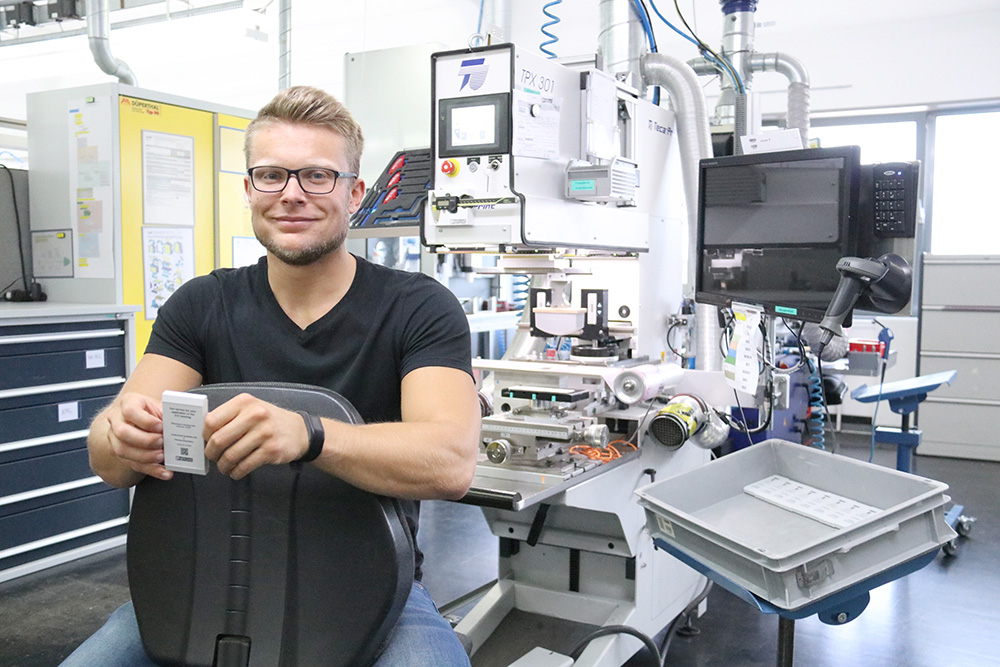