Bakterien lieben frischen Sauerstoff. Vor allem, wenn sie Schwerstarbeit in der Abwasseraufbereitung zu verrichten haben. Air Liquide entwickelt Anlagen, die den winzigen Mitarbeitern das Leben leichter machen sollen.
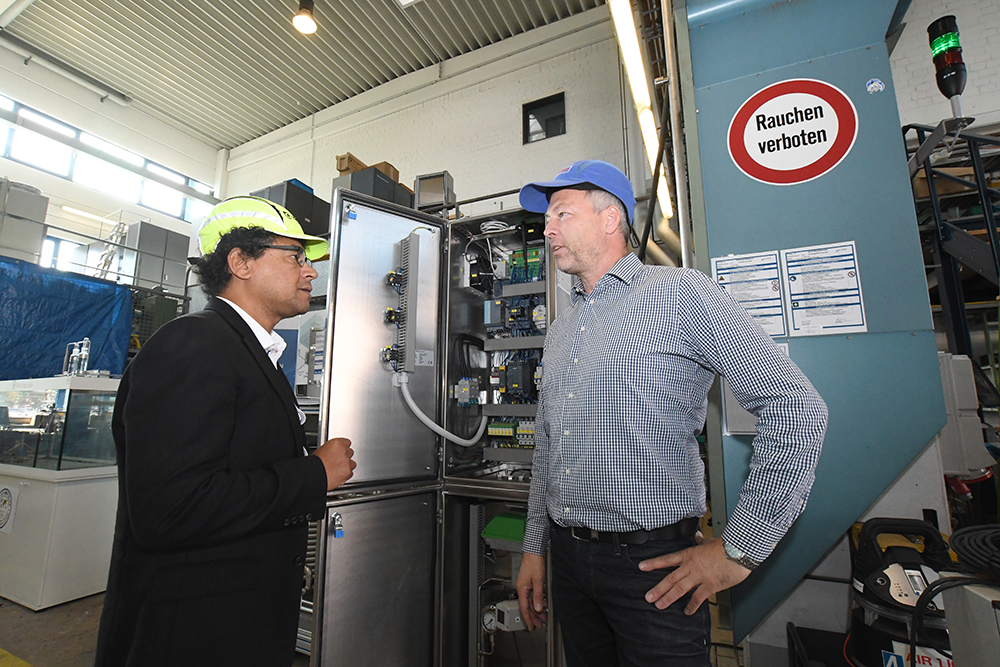
Lahcen Damou und Ulrich Butz
Wer Abwasser aufbereiten will, muss reichlich Knowhow haben, sowohl von den Maschinen als auch den Prozessen in den Anlagen, in denen das Wasser gebraucht wird. Denn das Abwasser soll frei von Rückständen sein, wenn es wieder in den normalen Wasserkreislauf zurückgeführt wird. Neben der mechanischen Reinigung durch Siebe und der physikalisch-chemischen durch Ausfällung gibt es zudem eine biologische Komponente bei der Aufbereitung. Eine zentrale Rolle beim Abbau von Schad- und Schmutzstoffen spielen winzige Bakterien, die sich in den großen Abwassertanks über ansonsten Ungenießbares hermachen.
Bakterienwellness
Air Liquide ist ein global agierender Konzern, der unter anderem mit flüssigen Gasen, hauptsächlich Stickstoff und Sauerstoff, umgeht. Die trifft man fast überall an, vor allem aber rund um große Chemieparks. Zum einen dienen sie als Grundlage in der Produktion. Doch Air Liquide betreut seine Kunden auch, wenn es um die Behandlung anfallender Abfallprodukte geht.
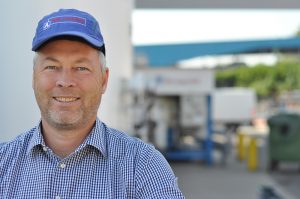
Ulrich Butz ist einer der Experten, wenn es um die Aufbereitung von verschmutztem Wasser geht. Der Maschinenbauingenieur gehört zu einem weltweit tätigen Team, die ihre Kunden mit innovativen Verfahren und eigenen Maschinen unterstützen. „Ein zentrales Element unserer Tätigkeit ist es, den Bakterien in den Abwassertanks den nötigen Sauerstoff in ausreichender Konzentration zuzuführen.“ Denn geht den kleinen Helfern die Puste aus, droht im schlimmsten Fall sogar ein Anlagenstillstand, da das Abwasser nicht entsorgt werden kann. „Dabei muss neben dem Sauerstoffgehalt und der Temperatur im Abwasserbecken auch die versorgende Pumpe des Injektors überwacht werden.“
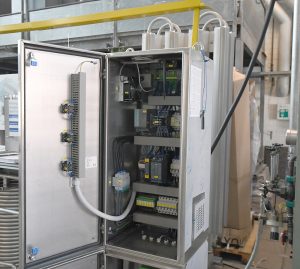
„Unsere Kunden kommen vor allem aus der chemischen und petrochemischen Industrie. Wir betreuen aber auch kommunale Kläranlagen“, beschreibt Butz seinen Kundenkreis. Die Anlagen können dabei enorme Dimensionen einnehmen: „Eines der größten aktuellen Projekte ist ein Chemiepark im niederländischen Stein, wo wir drei große Abwasserbecken mit je 114 Metern Durchmesser mit unseren Systemen bestückt haben.“ In jedem Becken sorgen fünf Injektoren für bakteriengerechte Sauerstoffverhältnisse – insgesamt 15 modular aufgebaute Anlagen sind auf die drei riesigen Tanks verteilt.
Handfeste Modularität
„Jeder unserer Injektoren hat einen eigenen Schaltschrank. Die Modularität ist bei diesen großen Anlagen extrem wichtig. In jedem der 15 Module verarbeitet eine Steuerung von Phoenix Contact die anfallenden Daten der verschiedenen Sensoren und sendet sie an das zentrale Leitsystem weiter.“ Was früher mit kompakten Prozessreglern und tausenden Relais bewältigt wurde, verarbeitet jetzt eine einzelne SPS-Steuerung pro Modul. Muss bei einem Tank, etwa wegen Wartungsarbeiten, der Füllstand verringert werden, dann können einzelne Module einfach abgeschaltet werden, ohne dass die Gesamtanlage dadurch beeinträchtigt wird.
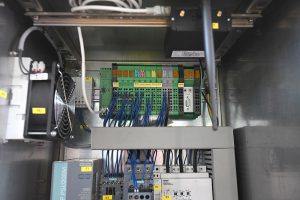
Lahcen Damou, betreuender Industriemanager von Phoenix Contact, ergänzt: „Die Prozesse werden nicht nur durch weniger Bauteile verschlankt und sicherer gemacht. Zusätzlich stehen jetzt deutlich mehr Daten zur Verfügung, die etwa für Wartungspläne genutzt werden können.“ Und auch dem Thema des Fernzugriffs per Remote Steuerung kann Ulrich Butz nur Positives abgewinnen: „Die Anlagen haben wir nur durch eine ganz intensive Zusammenarbeit mit Phoenix Contact überhaupt ans Leitsystem des Chemieparks anschließen können. Das hätte vor Ort etliche Mann-Tage gekostet und war so überhaupt kein Problem.“
Von wegen konservativ!
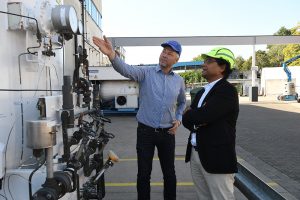
Keine Berührungsängste beim Umgang mit Modularität, SPS-Technologie und Remote Control? Ulrich Butz schmunzelt: „In der Chemieindustrie steht die Sicherheit an erster Stelle. Da sind wir natürlich eher konservativ. Aber die Welt dreht sich ja auch bei uns weiter. Und mit den neuen technologischen Möglichkeiten erhöht sich der Service, und der Anlagenbetrieb wird deutlich wirtschaftlicher. Grundlage unserer Innovationsfreude ist allerdings das Vertrauen in unsere Zulieferer, wie hier Phoenix Contact. Und da hat die offene und lösungsorientierte Zusammenarbeit auch auf dem kleinen Dienstweg bestens geklappt.“ (lo)