Vor 100 Jahren begann das Unternehmen von Hugo Knümann mit dem Vertrieb von Fahrdrahtarmaturen für Straßenbahnen. Seit dieser Zeit beeinflusst die technische Kombination aus isolierendem Material und leitendem Metall die Geschicke von Phoenix Contact.
Wieso eigentlich Keramik? Was ist an dem Material so besonders, dass es jahrzehntelang für die Trennung von Leitern und ihrer Umgebung taugte? Wird Keramik auch heute noch bei Phoenix Contact eingesetzt? Und gibt es Technologien, die aus dem Werkstoff noch mehr herauskitzeln?
Matsch und Pampe
Am Anfang wird gemischt, und zwar Ton und Lehm mit Wasser. Ton ist ein durch Witterungseinflüsse fein zermahlener Steinstaub Wenn man den mit Wasser versetzt, wird er formbar. Diese Rohmasse ist seit etwa 15.000 Jahren Ausgangsmaterial für allerlei Nützliches, von Teller zu Tasse, von Krug zu … Klemme.
In der vorindustriellen Zeit formte man den groben Ton auf einer Töpferscheibe oder per Hand. Dabei entdeckten die Handwerker: Je feiner die Ausgangsmaterialien gereinigt und gesiebt werden, desto hochwertiger werden auch die keramischen Erzeugnisse. Bei Porzellan kommen besonders reine Tonerden zum Zug, die einen hohen Anteil an Kaolin aufweisen. Kaolin ist ein sehr feines, weißes Gestein ohne Eisenanteil. Es enthält Kaolinit, das aus der Verwitterung von Feldspat entsteht.
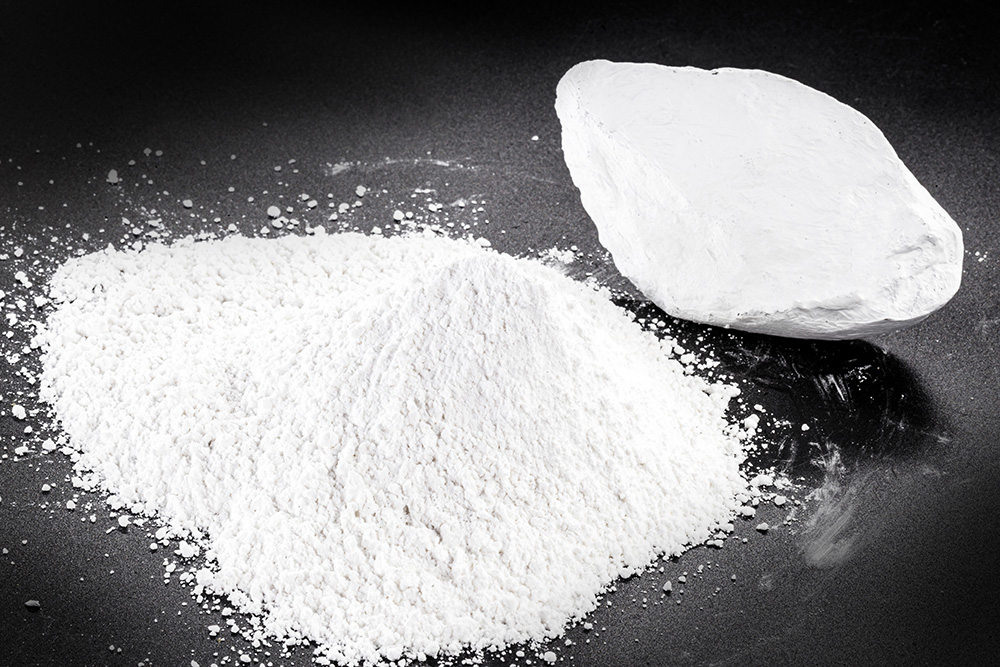
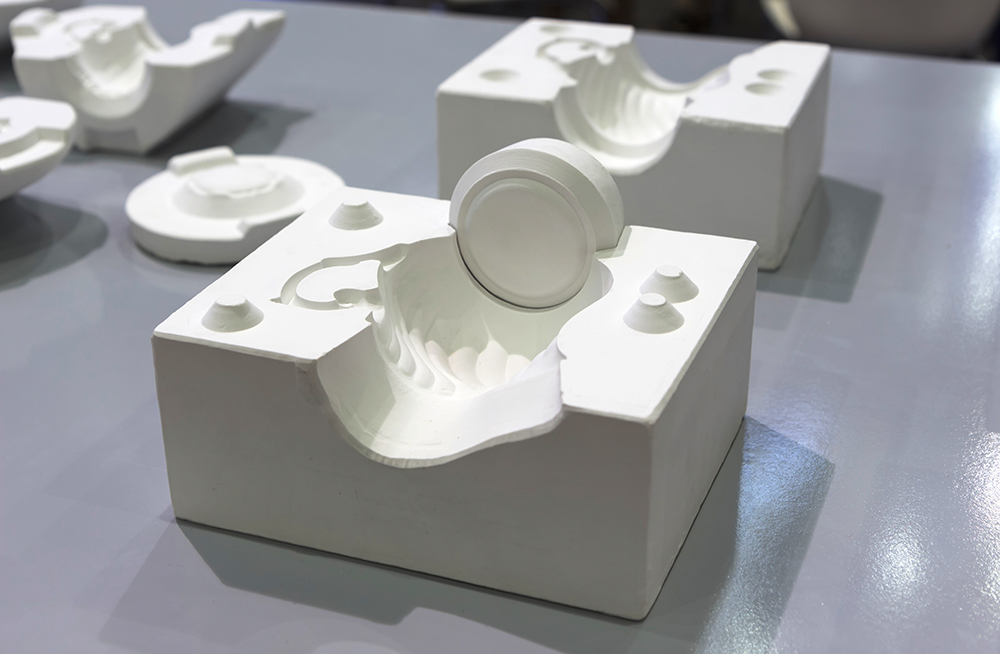
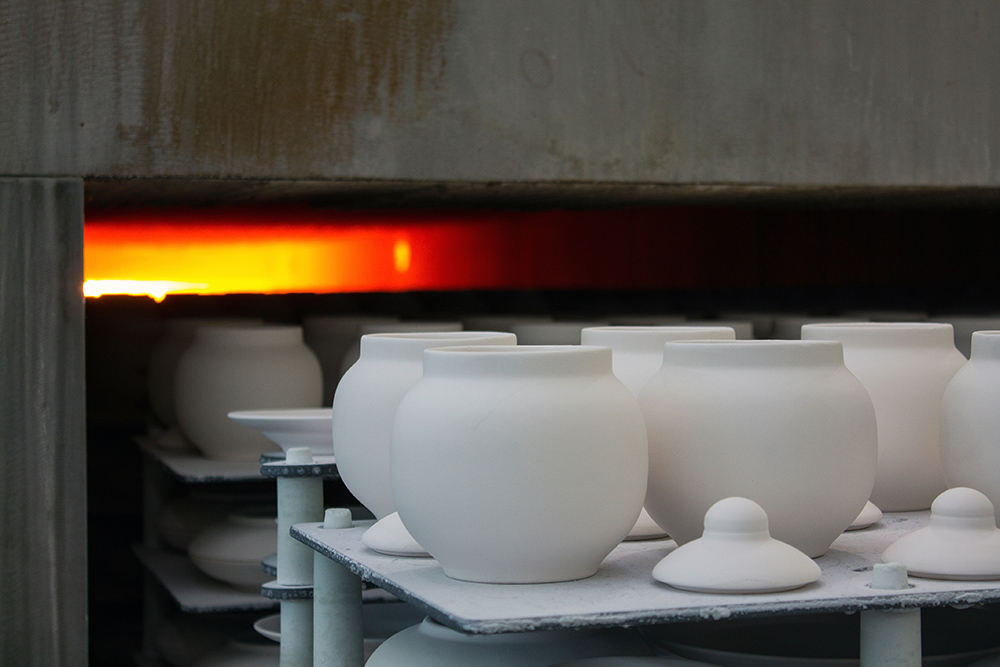
In der industriellen oder technischen Keramikverarbeitung wird der „Schlicker“, eine Mischung aus Ton, Wasser und weiteren Zuschlägen, in Gipsformen gegossen. Nach der ersten Trocknung wird der Rohling aus der Form genommen und bei etwa 1.000 °C zum ersten Mal gebrannt. Danach wird das noch poröse Werkstück mit einer Glasur versehen, die aus Quarz, Feldspat, etwas Kaolin und verschiedenen Flussmitteln besteht. Im folgenden 1.450 °C heißen Glattbrand schmilzt die Glasur und füllt den groben Untergrund. Die Glasur verbindet sich dauerhaft mit dem Porzellan. Der gesamte Körper schwindet dabei um rund 20 Prozent.
Dieser Schwund muss bei der Erstellung der Formen mit einberechnet werden. Diesen Vorgang nennt man Sintern. Das Wasser verlässt den sogenannten Grünling. Die körnigen Bestandteile schmiegen sich quasi Molekül für Molekül eng aneinander, verbinden sich aber chemisch nicht. Das Werkstück verdichtet sich und schrumpft, je nach Mischung des Schlickers unterschiedlich stark. Die molekulare Struktur ergibt eine extrem hohe Festigkeit. Die glatte Oberfläche ist unempfindlich gegen äußere Einflüsse. Und der Werkstoff Keramik isoliert hervorragend gegen elektrische Ladung. Kein Wunder, dass Klemmen jahrzehntelang aus dem harten Material gefertigt wurden und auch ebenso lange haltbar sind.
Der Werkstoff wird auch im Produktportfolio von Phoenix Contact noch immer genutzt. Das zeigen die Hochtemperaturklemmen der Produktfamilie SSK, deren keramischer Grundkörper vom Hersteller Ceram Tec in Plochingen gefertigt wird. Die Schwaben sind spezialisiert auf Hightech-Keramiken und entwickeln Technologien und Einsatzgebiete stetig weiter. Die keramischen Klemmen von Phoenix Contact kommen überall dort zum Einsatz, wo extreme Bedingungen dem heute gebräuchlichen Kunststoff ein schnelles Ende bereiten würden.
Klemmen und Scannen
Mittlerweile gibt es die Möglichkeit, keramische Werkstücke auch durch additive Fertigung herzustellen. Bei der Recherche zu diesem Beitrag reifte die Idee: Das müsste doch auch mit einem Muster der RWE-Phönix-Klemme klappen. Wo wir doch mit Protiq, einem Spezialisten der additiven Fertigung, eine Ausgründung aus dem Phoenix Contact-eigenen Werkzeugbau quasi vor der Firmentür haben …
Das Einscannen des Objekts der Begierde ist der erste Arbeitsgang. Das wird per hauseigenem 3D-Scanner im Werkzeugbau von Phoenix Contact erledigt. Vorsichtig nimmt Techniker Marco Schmidt die originale Klemme aus dem Jahr 1942 in Empfang. Normalerweise sind Materialprüfungen und Fehlersuche bei Reklamationsfällen sein Aufgabengebiet, doch heute steht die historische Klemme im Mittelpunkt des scannenden Interesses. Ihm zur Seite steht ein Hochleistungsscanner, der ähnlich einem medizinischen Computertomographen die Objekte rotieren lässt und dabei mit Röntgenstrahlen durchleuchtet. Eine Kamera macht fortwährend Aufnahmen, die sich dann am Computer zu einem dreidimensionalen Abbild des Museumsstücks zusammenfügen. Nach 50 Minuten sind 2.160 Bilder zu einem Datensatz verschmolzen, der digitale Zwilling ist geboren.
Jetzt geht es zum Marktplatz. Protiq hat nämlich einen virtuelle Plattform geschaffen, auf der Anbieter und Kunden der additiven Fertigung zueinanderfinden. Hier wird der 3D-Datensatz hochgeladen. Schnell noch das gewünschte Material eingegeben, in diesem Fall Keramik, schon erhält man nicht nur eine Liste der Firmen, die die Klemme fertigen können. Eine künstliche Intelligenz im Hintergrund berechnet anhand der Daten auch gleich einen verbindlichen Preis. Perfekter Kundendienst!
Feinarbeit am Zwilling
Der Auftrag geht nach Augsburg, zur Firma CADdent GmbH. Entstanden aus einem Dentallabor, fertigen dort 160 Spezialisten neben alltäglichem Zahnersatz auch Prototypen für die Industrie. Hierher wandert der digitale Zwilling und wird zunächst angepasst. Denn damit er wieder zum echten Leben zurück gedruckt werden kann, muss man die Besonderheiten des Herstellungsprozesses von Keramik kennen.
Stephan Seitz, bei CADdent für Forschung und Entwicklung zuständig, erklärt: „Zunächst einmal müssen wir das Datenmodell ungefähr 25 Prozent größer rechnen, damit der Rohling um diesen Faktor größer wird. Denn das Material schwindet, wie immer bei der Sinterung einer Keramik. Materialkunde ist für uns entscheidend. Wir wissen genau, um wieviel kleiner der Rohling wird. Das ist unser Knowhow.
Dann ist es wichtig, möglichst einheitliche Wandstärken zu erreichen, damit beim Trocknen keine Spannungsunterschiede im Keramikkörper für spätere Risse sorgen. Daher sind auch in den massiv erscheinenden Bereichen Hohlräume vorgesehen. Und zu guter Letzt vermeiden wir scharfe Kanten, denn auch hier sorgt die Schrumpfung während der Sinterung für mögliche Rissbildungen.“
Bei dieser Schilderung ahnt man, wie intensiv sich die Experten von CADdent mit den Werkstoffen auskennen müssen, die verarbeitet werden. Neben Keramik werden hier in Augsburg auch Titan, Cobalt-Chrom, Kunststoff und Gold gedruckt.
Mal „eben schnell“ geht es nach den Rechenkünsten dann auch nicht weiter: Sieben Stunden lang wird mit jeweils 25 Mikrometer Schichtstärke der flüssige Keramikschlicker zur fertigen Klemme aufgebaut. „Dieser Schlicker ist speziell abgestimmt auf das LED-Modul des Keramikdruckers. In ihm enthalten ist ein Flüssigkunststoff, der lichtempfindlich ist. Das LED-Modul belichtet das Material selektiv, wodurch der lichtempfindliche Teil des Kunststoffs aushärtet und die darin enthaltenen Keramikpartikel umschließt.“
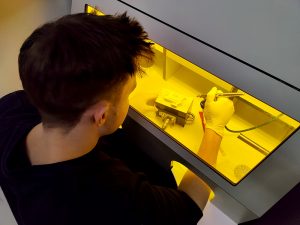
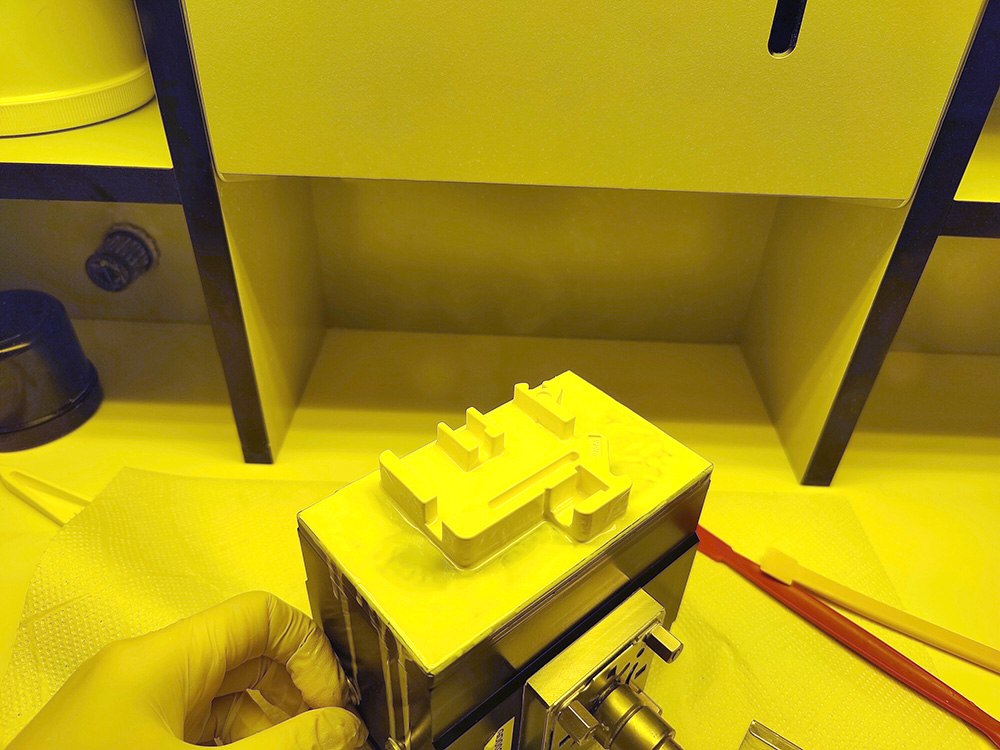
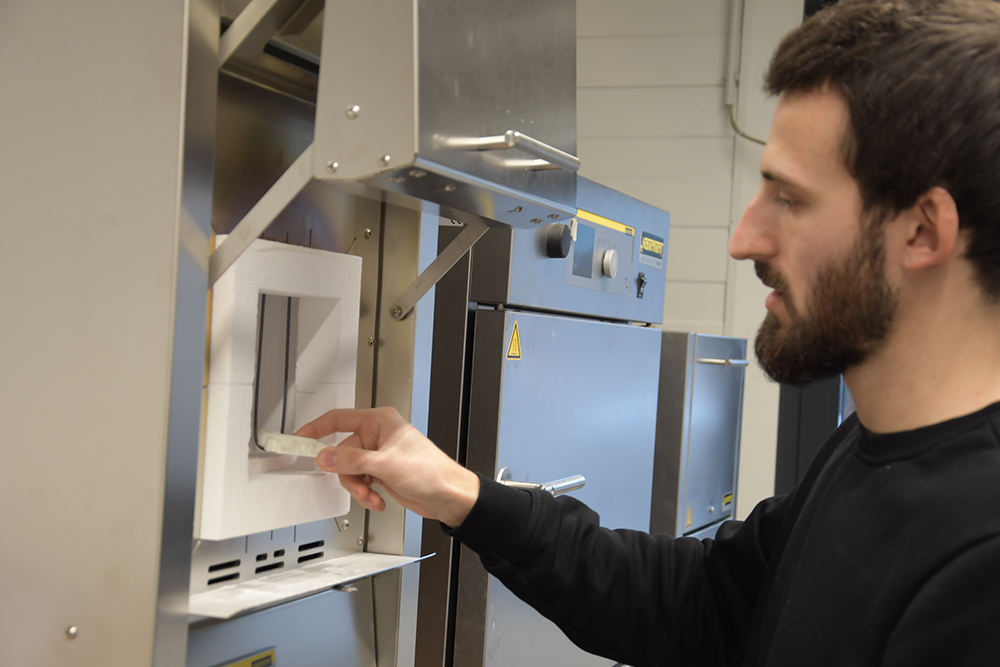
Ein Klotz ohne Ecken und Kanten
Anschließend geht es in die erste Wärmebehandlung, in der der Kunststoff ausgebrannt wird. Danach geht es zum zweiten Mal in einen Ofen, in dem das eigentliche Sintern stattfindet. Die entstandenen Mikroporen schließen sich, der Grünling schrumpft auf seine exakte Größe.
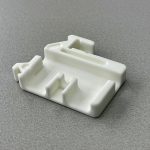
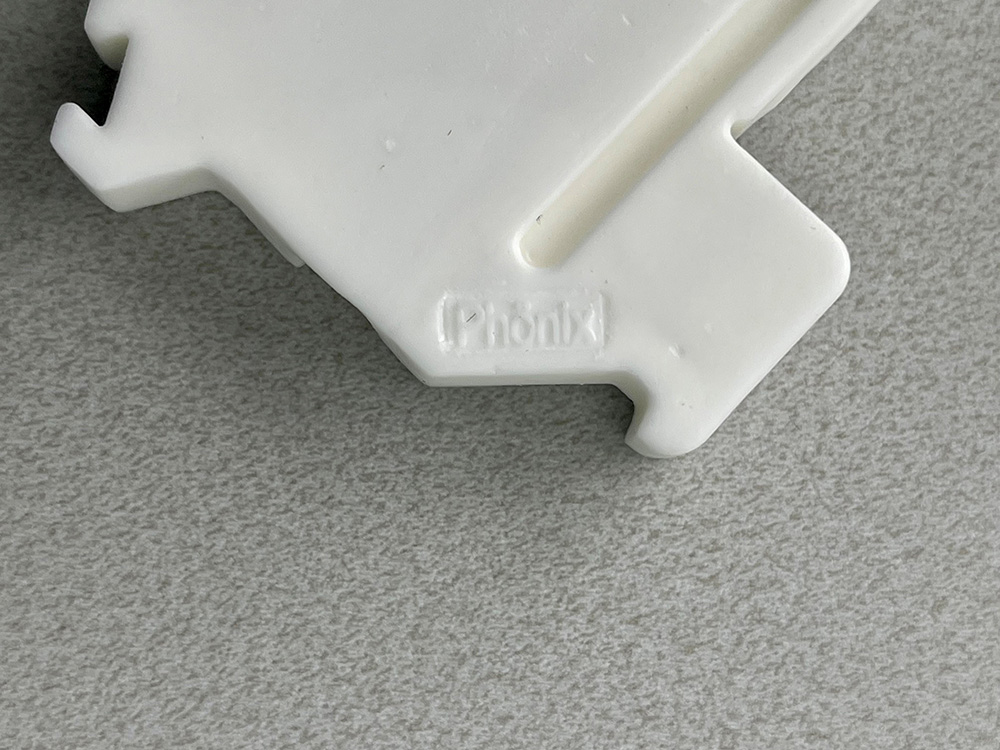
Stephan Seitz präsentiert das Ergebnis der Anstrengungen. Die neue Klemme glänzt fast wie Zahnersatz und ist überraschend schwer. Wie angekündigt sind die Kanten abgerundet. Ansonsten sind alt und neu komplett deckungsgleich. Selbst der Phönix-Schriftzug mit dem typischen „ö“ ist nicht verlorengegangen.
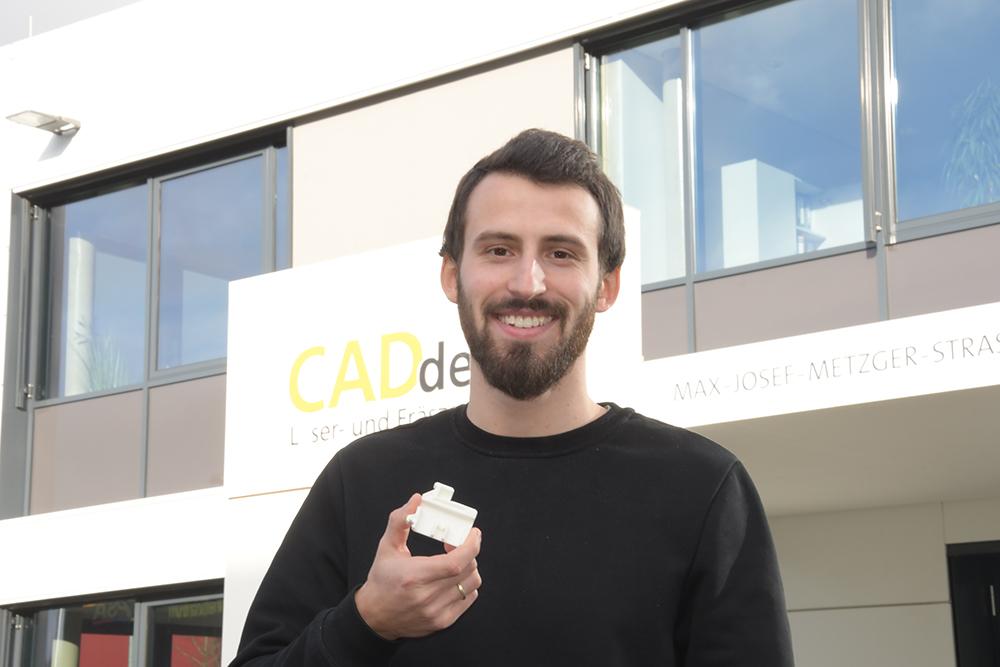
Davon überzeugt sich wenig später auch Marco Schmidt im Werkzeugbau von Phoenix Contact, bei dem die Reise in die digitalen Welten der Klemme begann. Ob als digitaler Zwilling und 3D-Druck oder als gegossene und gepresste Variante – die Reihenklemme ist auch in ihrem Urmaterial nach wie vor ein Dauerbrenner!