1,500 cubickilometers (!) of wastewater are produced worldwide every year. An enormous amount that, if not treated appropriately, will jeopardize the global drinking water cycle in the long term. In Constance on Lake Constance, risks and solutions to this problem are omnipresent.
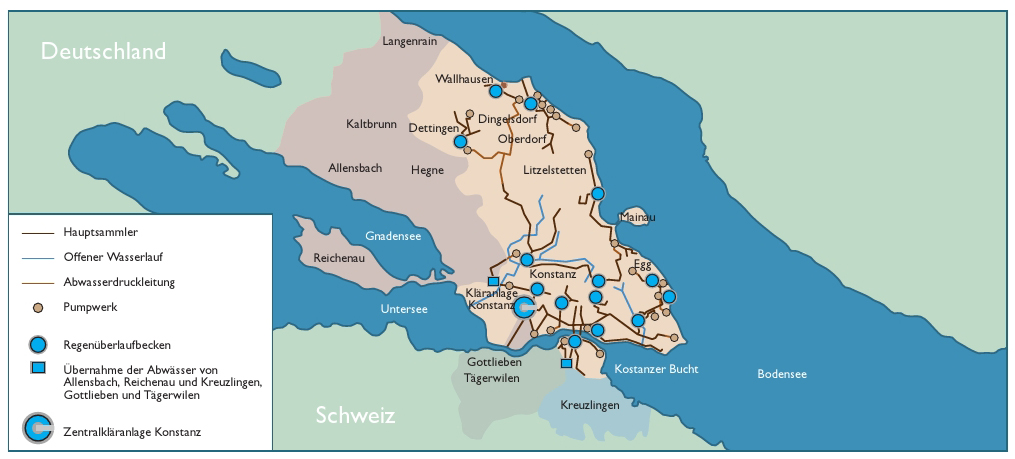
Today, around 35 percent of all people worldwide have no access to clean drinking water. Until a few decades ago, poor water quality was also a problem at Lake Constance. Until well into the 1960s, wastewater flowed largely untreated into the Mare Suebicum, which serves as a drinking water reservoir for the entire region.
In the 1950s, phosphorus levels began to rise dramatically. New artificial fertilizers, the triumph of water-flushed toilets and the mass distribution of washing machines and dishwashers created a completely new wastewater situation. In addition, the population around Lake Constance increased significantly. Industrial and slaughterhouse wastewater entered the lake untreated. The result was massive algae blooms that deprived the lake of oxygen and almost caused it to overturn several times.
In 1959, the International Water Protection Commission was founded to coordinate the wastewater treatment of the riparian states. There it was decided that sewage treatment plants and sewers should protect Lake Constance. The first stage of the Constance central sewage treatment plant went into operation in 1966. It was not until 1968 that the biological treatment stage was ceremoniously inaugurated. But it was to take another 20 years before Lake Constance was no longer threatened by algae blooms and biological desolation.
Waste water in, drinking water out
In the meantime, the situation has improved considerably. And this despite the discharge of the previously treated wastewater. This requires particularly thorough cleaning so that the wastewater does not become a problem for the liquid food. The waste disposal companies of the city of Constance are responsible for this task.
The Entsorgungsbetriebe Stadt Konstanz (EBK) is the largest municipal waste disposal company in the Lake Constance region. The approximately 110 employees focus on waste management as well as wastewater discharge and treatment. The central wastewater treatment plant treats up to 40 million liters of wastewater per day, which is generated in the Constance district, the municipalities of Allensbach and Reichenau, and the Swiss town of Kreuzlingen and the municipalities of Tägerwilen and Gottlieben there. This corresponds to about 175,000 population equivalents. On its way from the polluter to the wastewater treatment plant, the wastewater has to overcome large distances in the approximately 295-kilometer sewer network as well as differences in altitude. To do this, 26 pumping stations are used. The rainwater is collected and treated in 16 rainwater treatment plants and four rainwater clarifiers before it is discharged into Lake Constance.
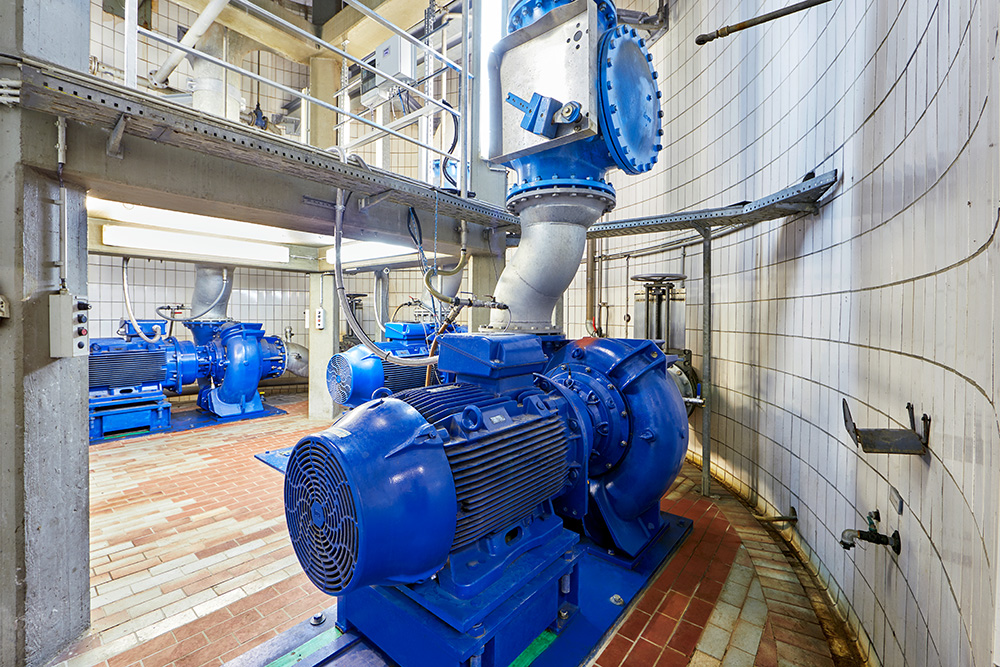
Heavy-duty work for an assembly that is indispensable when water has to be routed through pipes and basins: Four large hidrostal pumps, each with 75 KW of power, operate at the intake pumping station in Constance when it is dry, as well as three other powerful pumps during rainy weather. At least one of the four heavy-duty pumps is always running, i.e. 24 hours a day, seven days a week. The energy required for this is considerable: the pumps need around 560 megawatts of energy for their pumping activities.
Keep the overview
This is where the experts from Phoenix Contact, who were tasked with improving the efficiency of the overall system, came in: energy consumption and maintenance monitoring. If optimization were to take place here, the greatest amount of energy could be saved.
Electrical engineering master Thomas Geiz, who works in PxC’s water management solution sales department, explains: “We didn’t just look at the efficiency of the pump and drive motor. We first looked at the system efficiency. At what operating point is the ratio of electrical power supplied to the volume of wastewater pumped the best? In addition to the efficiency of the pump and motor, aspects such as the pipe routing, the suction pressure of the pump and other mechanical and hydraulic conditions also play an important role in such a consideration.
Then there is the availability of the pumps and the maintenance and servicing required to keep them running 24/7. In recent years, there have been costly repairs to the pumps. We have only been able to clarify the cause to a limited extent.”
The “PumpMonitor” is a ready-to-install control cabinet solution that provides holistic monitoring of pumps and motors and increases efficiency. As part of condition monitoring, the system evaluates mechanical, hydraulic and electrical wear indicators.
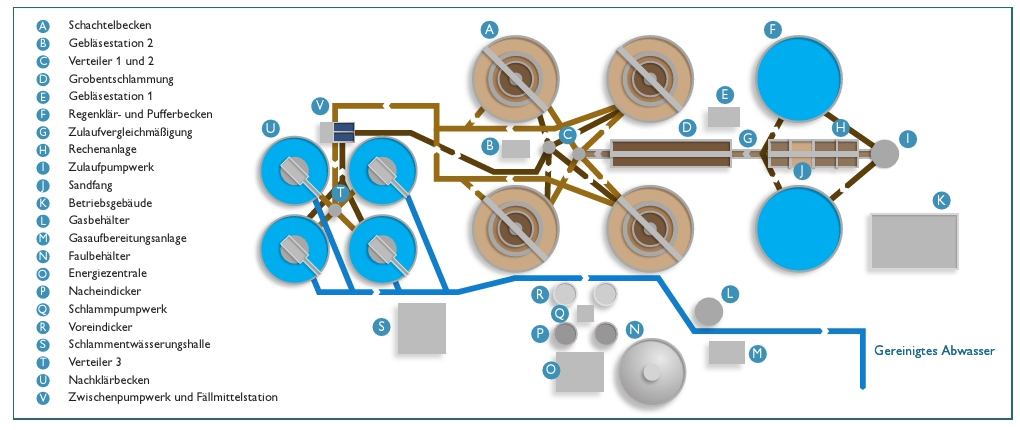
Hartmut Appelt, head of wastewater chemistry at the EBK, points out another important advantage of the PumpMonitor: “We activated the efficiency monitoring by means of a measurement during operation and immediately recorded the current status of the pumps. The system is therefore suitable for a plant with existing pumps. After determining the best operating point and efficiency of the system, the values are displayed to us as an immediately interpretable traffic light and absolute number.”
Monitoring step by step
Expert Geiz continues: “Starting from this point, it is now possible to monitor how the plant changes during its lifetime. In addition, the operating personnel are informed as soon as the efficiency deteriorates. The evaluation of these parameters as well as the status variables is carried out directly in PumpMonitor, so that the EBK employees always have a simple overview of the status of the pumps thanks to the traffic light display. If a change occurs here or in efficiency, they can see exactly what the reason is in the expanded view.”
In a first step, one of the dry weather pumps was equipped with the monitoring system to gain practical experience. The test phase went smoothly, and in the meantime the other pumps are also secured and monitored with “their” PumpMonitor.
The EBK employees independently integrated the solution into the process control system of the wastewater treatment plant. From the possible communication standards – such as OPC, Modbus TCP or Profinet – they decided on the Profinet protocol. Since there is a documented and defined data structure for transferring the information from the PumpMonitor system, the implementation was simplified. “The possibility of using sample programs on the higher-level controller from Phoenix Contact, which acts as a Profinet master, as part of the programming also helped to speed up the implementation of the task,” reports Appelt. Because the wastewater treatment plant has an automation system with Profinet functionality from Phoenix Contact, this was the easiest way into the control room.
Thus armed, the people of Constance can look to the future with confidence when it comes to the cleanliness of their “Swabian Sea”.
Phoenix Contact Wasser- und Abwasserwirtschaft
Der PumpMonitor