Wie soll man an die Daten eines Kugellagers kommen, das sich in einem gigantischen Rührtopf befindet, in dem heiße Kunststoffsuppe schwappt? Mit diesem Kunststück beschäftigt sich eine Forschungsgruppe der TU Dresden in Zusammenarbeit mit BASF und Phoenix Contact.
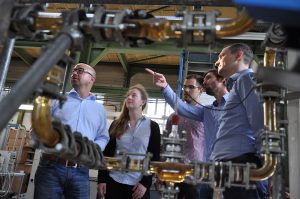
Am BASF-Standort Schwarzheide werden chemische Grundstoffe produziert. Mitten im Braunkohleabbaugebiet der Lausitz gelegen, wurde das Werk schon 1935 als Hydrierwerk Schwarzheide gegründet und diente zunächst der Herstellung von synthetischem Benzin aus Braunkohle. Heute gehört es zur BASF SE und dient seit 1972 vor allem der Polyurethanproduktion. Daneben werden technische Kunststoffe, Schaumstoffe, Pflanzenschutzmittel und Lacke hergestellt.
Auf keinen Fall Stillstand
Um aus den Basissubstanzen die jeweiligen Endprodukte zu synthetisieren, wird erhitzt, gekühlt, gerührt und gegossen. In mächtigen Rührkesseln werden die Inhaltsstoffe zusammengeführt und auf mehrere hundert Grad erhitzt. Sie sind ein zentraler Bestandteil der Produktion. Steht der Kessel, steht die Produktion. Dann wird es teuer.
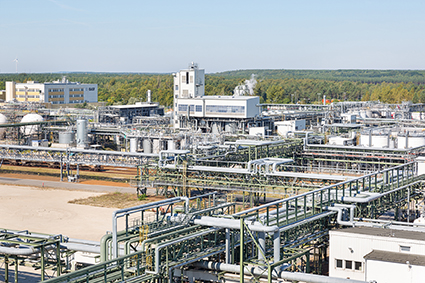
Das Rührwerk in diesen Kesseln wird durch extrem starke Kugellager beweglich gemacht. Diese Kugellager unterliegen einem normalen Verschleiß. Das Problem: Da die Rührwerke im Kessel sind, sind sie nicht zugänglich. Fällt das Kugellager aus, geschieht dies plötzlich und ohne Vorwarnung. Also müssen Wartungsroutinen, bei denen der Rührkessel inspiziert und das Lager bei Bedarf getauscht werden kann, nach einem starren Zeitschema ablaufen, welches immer kürzer ist als der tatsächliche Verschleiß, damit die Anlagen kontrolliert heruntergefahren werden können.
Wie schön wäre es, wenn man den Zustand des Lagers und damit die Stabilität des Prozesses genauer und zeitaktuell bestimmen könnte und die Produktion nur dann stillstehen müsste, wenn der Zustand des Kugellagers tatsächlich einen Tausch nötig machen würde? Doch wie an das Lager herankommen? Und welche Sensoren halten zuverlässig und jahrelang den Angriffen aggressiver Chemikalien unter Hitze und Druck stand?
Projekt gesucht
Und hier kommt die neue PLCnext Technology von Phoenix Contact ins Spiel. Denn diese systemoffene Steuerungstechnologie kann mit Hochsprache angesprochen werden. Und nicht nur das, moderne Softwaretools wie Matlab/Simulink können einfach in PLCnext integriert werden. Was zu beweisen war. Also galt es, im Zusammenhang mit den Aktivitäten zur diesjährigen NAMUR Hauptsitzung ein Projekt zu identifizieren, bei dem die PLCnext Technology konfrontiert wurde mit der Überwachung von Slow Rotating Equipment, einer ganz typischen Anwendung in der Prozessindustrie.
Jetzt kam Dresden auf den Plan: Denn der Leiter der Professur für Prozessleittechnik und der Arbeitsgruppe Systemverfahrenstechnik an der Technischen Universität Dresden, Professor Dr. Leon Urbas, kennt die Branche. Und er kennt Phoenix Contact. Er gab den richtigen Tipp mit dem heißen Kessel und seinem malträtierten, aber fast unerreichbaren Lager.
Dr. Markus Graube ist der verantwortliche Wissenschaftler im Labor „Process-To-Order“ am Institut. Das gilt in Deutschland als führend, wenn es um „modellbasierte, datengetriebene und informationstechnische Ansätze zur Beschreibung und der Vorhersage des Verhaltens modularer Anlagen“ geht. Einfacher ausgedrückt: Die Wissenschaftler wollen mithilfe von Daten Voraussagen treffen über den Zustand von Anlagen. Quasi in den Kessel gucken, ohne hinein fassen zu müssen.
Damit sind sie ideale Partner der PLCnext Technology. Denn die Studierenden setzen auf Hochsprachen, um die Algorithmen zu programmieren, mit denen Steuerungen aus den gewonnenen Daten Voraussagen gewinnen und Handlungen wie Alarme oder die Reduzierung von Drehzahlen ableiten. Die Programmierung in Maschinensprache, mit der klassische Steuerungen arbeiten, wäre viel zu aufwändig und teuer.
Fachsimpeln am Schaltschrank Arbeiten an und mit der PLCnext Die Steuerung „versteht“ Hochsprache Die Forscher entwickeln Datenmodelle für Predictive Maintenancevon Algorithmen … Dazu verwenden sie Matlab Simulink Die TU Dresden setzt auf Nähe zur Praxis Anderes Projekt, genauso faszinierend – ein Algenreaktor
Ideale Partner
In Zusammenarbeit mit den Spezialisten von Phoenix Contact entwickelten Graube und sein Team einen komplexen Algorithmus, der aus der Stromaufnahme des E-Motors sowie der Temperatur und Stoffzusammensetzung im Kessel Rückschlüsse auf den Zustand des Kugellagers zulässt. Der mit Hilfe von Matlab/Simulink erstellte Algorithmus soll die Abweichungen, die vom defekten, schwergängigen Lager hervorgerufen werden, erkennen und vorwarnen, bevor das Lager ganz ausfällt. Das Aufspielen auf die Steuerung klappte problemlos.
Mittlerweile befindet sich der Schaltschrank mit der innovativen Steuerung vor Ort und zeichnet fleißig Daten auf, um so die angestrebte Predictive Maintenance zu ermöglichen. Einzig das Kugellager spielt noch nicht mit. Denn es läuft rund und liefert bisher noch keine Situation, die ein Eingreifen nötig macht und den Algorithmus lernen lässt. Aber da sind sich alle Beteiligten einig: Das kommt noch.