Through the tubes at 500 km/h – Swiss precision and Blomberg innovation are paving the way for the high-speed transportation of the future.
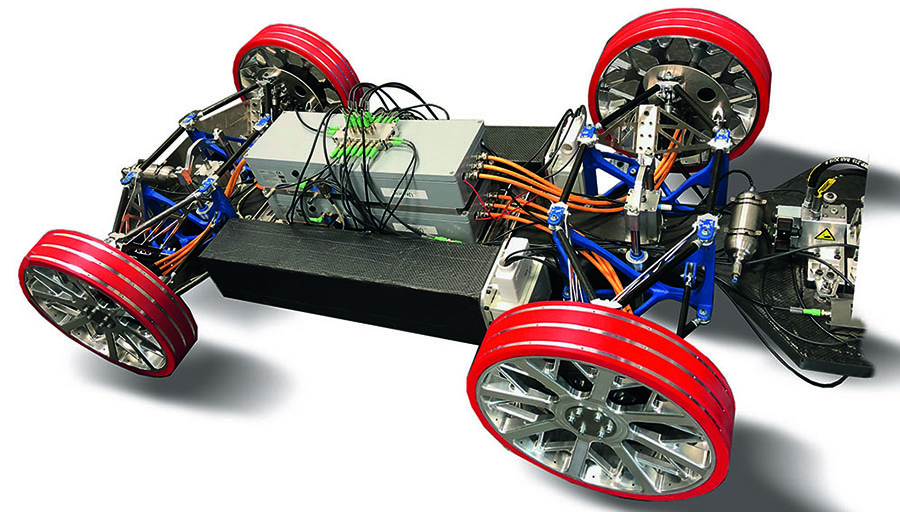
NCIS Zurich. It is not the banking district that is in the public eye this time, however, but the campus of ETH Zurich, the Swiss Federal Institute of Technology. This is where Swissloop – an innovation project at the highly prestigious international training and research center – is based.
The aim is to develop innovative technologies for fast, tube transportation systems with speeds of up to 1,200 km/h, in line with the Hyperloop vision of Tesla founder Elon Musk. The research on this and the modifications are carried out globally by different teams. Once a year, a major competition – the Hyperloop Pod Competition – is held at Musk’s company, SpaceX, in Los Angeles, where attendees demonstrate what their vehicles can do. Of the original (approximate) 1,000 teams who entered the competition in 2018, only 18 remained.
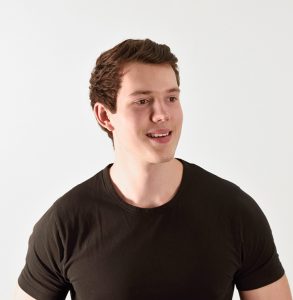
Following on from finishing third in 2017, the Swissloop team again set their sights on claiming one of the top spots in the 2018 competition. However, a problem with the motor controller in the vacuum tube thwarted the team’s expected leap onto the podium at the last second.
Hanno Kappen, still an Electrical Engineer student at ETH Zurich in 2018, was one of the 20 or so members of the student team that made up the 2018 development group.
Acceleration like a super-sports car
“The project vehicle, referred to as the pod, has to accelerate to the highest possible speed within a few seconds in the test tube of Musk’s company, SpaceX, and come to a stop in time,” explains Kappen. The race between the driverless pods is held in the USA in a SpaceX-developed “hypertube”, a partially evacuated tube that is 1.25 kilometers long and has a diameter of 1.8 meters. The vehicles are propelled along an I-rail that is anchored into the floor and which runs through the entire length of the tube. The requirement profile is reminiscent of dragster races: the winner is whoever reaches the highest maximum speed in the available distance – and at the same time manages not to crash at the end of the track.

The drive energy must be generated (without a combustion engine) on board the pod. The vehicle designed by Swissloop was powered with 250 kWh, supplied by batteries. The propulsion is generated by one 110 kW hub motor in each of the four wheels, which are coated with a special PU foam that enables high acceleration and braking forces to be transmitted. The “Mujinga” generates a total output of 540 PS.
The goal for the Swissloop team in 2018 was to reach a speed of around 500 km/h. This demands an average acceleration of around 12 m/s2 – a magnitude that is normally only achieved by super-sports
cars.
High-tech down to the last detail
“Teams from different disciplines have to work in very close cooperation in order to be able to achieve such speeds,” Hanno Kappen tells us. Experts from the fields of machine building, vehicle technology, electrical engineering / electronics, as well as hydraulics and pneumatics worked together on the pod.
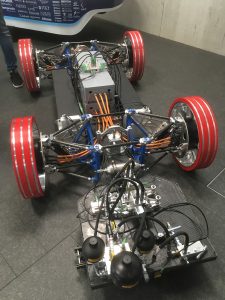
The entire vehicle is designed to be ultralight in construction. The chassis and a wide range of other
components are made of light construction materials such as carbon fiber and aluminum. The weight of every component was evaluated and every trick attempted in order to save just a few grams in one part or another. This approach is the only way possible to be able to keep the total weight within the
range of 300 kg despite the enormous power.
E-racer at Formula 1 level
“There were particular challenges in the area of the sensor technology, controllers, and actuators,” explains Kappen. Due to the high speeds, these components had to operate at the limits of their capabilities. At 500 km/h, even the slightest unevenness in the rail causes considerable impact forces on the wheels and the entire mechanism, which then have to be compensated for at lightning speed.
The axles, suspension, and absorbers must satisfy Formula 1 demands. The vehicle does not have steering. Directional changes have to be performed through minute readjustments to the individual wheel drives. Contact with the I-rail is particularly sensitive because this is done using small rollers, and not only on the side, but also vertically from below. These rollers are pressed onto the rail by spring and absorber links, and report positional deviations to the controller via sensors.
This then has to react in the millisecond range because the tolerances for rail deviation are extremely tight. Furthermore, the vertical rollers also have to apply controlled pressure forces to control the vertical inclination angle of the vehicle – such as during accelerating or braking.
Teamwork with the industry
“Without the support of a large number of companies, we would never have been able to complete this project,” admits Hanno Kappen. This was not only true for the large number of pod components, but also for the advice on the design and operation. Only advanced technology was utilized. His group, made up of four e-technology students, were given the task of overcoming all of the challenges faced in the field of energy supply and control. These included battery management, various electronic subsystems for sensors and actuators, and the development of the linkage network via which the flow of data and commands between the controller and the numerous peripheral units had to be managed.
Neural pathways in green
“It was of great value for our e-technology group to be able to call upon Phoenix Contact, which is known worldwide for its high quality, as a partner for the electrical networking,” says Kappen. Furthermore, Phoenix Contact also engaged in intensive consulting and support. “From this, it became apparent that the M12 circular connector was best suited for our application.” The team members were also able to assemble the multi-position cables themselves where needed.
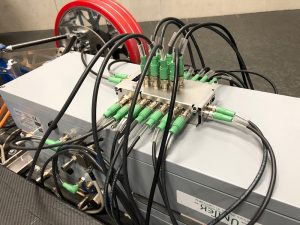
For this, Phoenix Contact also promptly delivered the suitable cable material. Due to the green end caps, these “neural pathways” are clear to see, in particular in the central network controller PCB developed by Kappen, which has a total of 20 multi-position communication connections. “I was particularly impressed at how the company was able to provide fast, non-bureaucratic, and above all very professional assistance through its local Swiss branch,” says Hanno Kappen, summarizing his experiences. Today, he lives and works in Los Angeles.
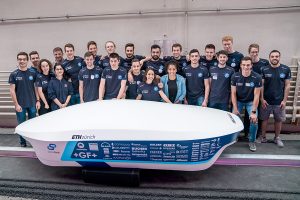
Naturally, the team from the Swiss Federal Institute of Technology in Zurich do not want to give in after the ignominy of the technical knockout of 2018, and have long since been working on improvements and the next attempt. There is also a deeper aim, because as a land of tunnels, Switzerland is also planning its own version of the evacuated high-speed tube, and will need suitable vehicles.