When one of Europe’s most innovative planning and consulting firms in the real estate sector constructs its own building, the extraordinary becomes the standard: At OWP12, innovation begins far below the floor slab. The new Drees & Sommer office building is fascinating down to the last detail. And makes it unmistakably clear: In the future, building will be very different!
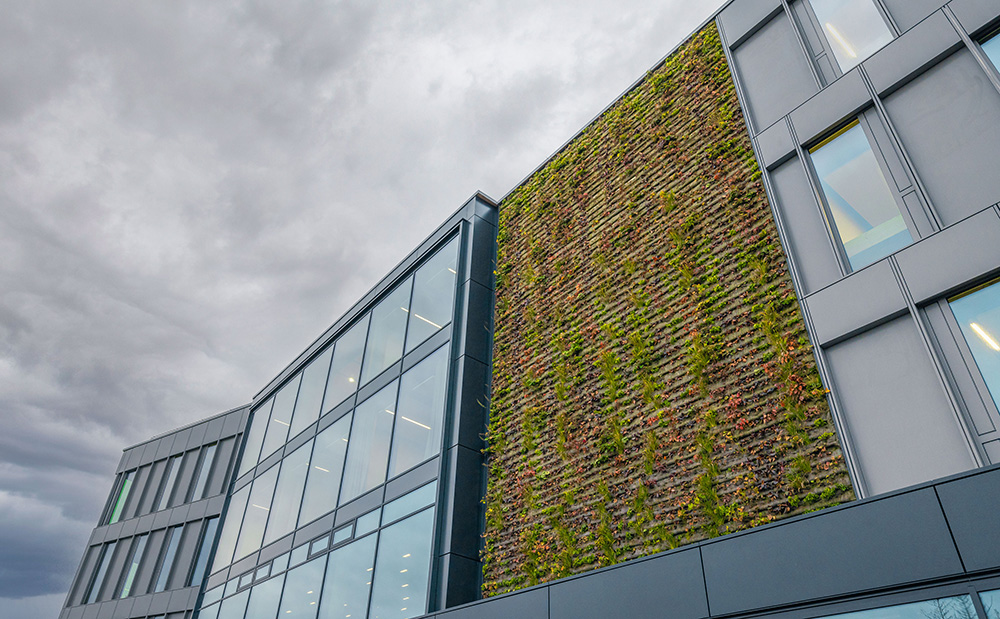
The most photographed component of OWP12 is in the central part of the facade. A vertical flower meadow is just still exotic, although many planners and decision-makers want that to change significantly in the coming years. OWP is short for “Obere Waldplätze” and describes a street in the Stuttgarter Viertel Vaihingen.
But before the autumn-colored natural façade can be admired in itself, a parking space has to be found. More than 4,000 employees work for the international consulting firm for the construction and real estate sector, 1,100 of them on site at the company headquarters alone. The way to the first meeting leads past the construction site.
Practice what you preach
Steffen Szeidl is one of three board members of Drees & Sommer and explains why we are facing a game changer in the construction industry: “We have grown strongly in recent years. Three years ago, therefore, the decision was made to construct another building on the Drees & Sommer campus. Even before Corona, we had equipped our existing office landscapes with state-of-the-art media technology and created the conditions for hybrid working between home office and office.
The new building now offers everything that the home office cannot or cannot always provide: Spaces for concentration, communication and cooperation in the individual teams. And with this new building, we naturally want to set the best example for our customers as well, creating a sustainable and digital blueprint for office buildings of the future. Practice what you preach.”
With an amused sigh, the company boss explains: “As a consulting firm specializing in construction and real estate, the demands on our own project are naturally particularly high. Not only from our experts in civil and industrial engineering. In the same way, we employ experts from various disciplines such as chemistry, design, psychology or ecology. And reconciling the requirements of so many disciplines in our building was not always easy, so we are all the more proud of the result.”
The way to the lighthouse
Drees & Sommer’s new heart starts out as a PlusEnergy building, i.e. it is intended to generate more energy than it consumes. Thomas Berner, the project manager for OWP12, joins the conversation. He explains why the innovation starts under the very first layer of concrete: “We started with the issue of sustainability. Very quickly it was clear that we wanted to use geothermal energy. 22 boreholes are located under the building and supply OWP12 with heat. In addition, there is an innovative photovoltaic façade on the south and west sides. The theme of energy generation continues through the roof. With this, however, it was clear that we could not create enough green roof space. That’s how the idea for our Eye Catcher came about – the green façade immediately catches the eye.”
The experienced civil engineer describes what the hanging gardens of Vaihingen are all about: “We didn’t want mosses and brown plants, but a flowering, invigorating ensemble in all seasons. On the north side, that’s not so easy, especially on such a large area over several floors. But with a carefully crafted planting plan, the wall grows and thrives beautifully. The green curtain provides a temperature delta of around 4 to 5 degrees, warmer in winter, cooler in summer.” Berner describes, not without pride, that Stuttgart requires green facades on commercial buildings in new development plans, but that there has been little experience with them. “That’s where we are real pioneers. Together with the companies involved, we have implemented new developments.”
Thick is dumb
Walking around the building, we reach the south side. There is only a little more than 20 meters between the building and the noise, because this is where the A 831 six-lane highway runs along. Thomas Berner points to the next innovation. “This is a real world premiere. The facade here consists of modules. Suitable for high-rise buildings. Durable. With perfect sound insulation. And equipped with solar cells.” Together with the companies FKN and Evonik developed these vacuum-insulated panels with superior properties. The experts have designed the elements in such a way that vacuum insulation loses its supposed sensitivity. “We expect the panels to last at least 40 years.”
Company boss Szeidl adds that the modules are cradle-to-cradle capable, i.e. they can be broken down into their components and the materials can be reused. Unaffordable high-tech gimmick? Steffen Szeidl vigorously denies this: “The facade has a depth of just nine centimeters, including photovoltaics of only 21 centimeters, instead of 35 to 40 centimeters as with a standard facade. That creates several square meters more usable space. And that also makes these elements, which are about 20 percent more expensive, absolutely competitive in terms of cost.”
By the way: The sound insulation of the thin facade has been tested by the Institute for Window Technology Rosenheim and certified as exemplary. Szeidl comments: “The modules were registered and presented as a patent. Building authority approval has been available since last year as a facade suitable for high-rise buildings.”
House with bend and edge
Not only is the proximity to the highway a challenge, but so is the cut of the property itself. Szeidl describes it as banana-like. OWP12 also follows this shape in its floor plan. This results in three building elements. The middle section with the green facade represents the joint that connects the other two building sections and around which the building rotates.
In order to keep costs in check, the planners used a special trick, as Steffen Szeidl explains: “When it comes to construction, people always say that we only build one-offs. But that’s nonsense. If you look at automotive construction, for example, there are an extremely large number of variants possible, but they are all assembled from a manageable number of possible components. So we divided the building into smaller units in terms of planning and looked to see where we could have the same functionalities. How can we modularize as early as the planning stage? It’s not about the cheap square box. For that, we used a digital planning methodology that can translate any individual architectural design and all technical building concepts into modules.”
The company boss adds: “An obviously revolutionary idea, because if you look at new buildings all over Europe, we have about 80 percent individual pieces, and only 20 percent are standardized. We have to turn that around if we want to build faster, cheaper and more efficiently. You can see with our building that standardized modules are reused on every floor. So we end up with a property that is innovative and unusual, but on par with standard solutions in terms of lifecycle costs.”
Small thought – cleverly done
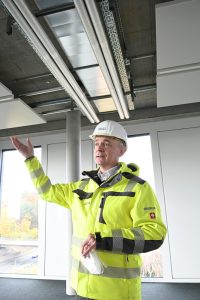
The idea of the module takes on a whole new dimension in OWP12, especially in the interior fittings. Berner begins by describing the standard: “First the planners draw up the requirements, then each individual trade goes out to tender, and as a rule the cheapest one is awarded the contract. In the standard, you have the shell, into which then comes heating, ventilation, cooling, sanitation – each with its own installation team, each with its own planning. So there’s a fair amount of tinkering and assembling on site.”
We meander past workmen and materials into the interior of OWP12 and work our way up to the fourth floor. “Up here, we are almost completely finished,” says Thomas Berner, describing the situation on site. The drywall is in place, the carpet has been laid, and the interior work is almost finished. Except for the ceiling, because the installations there are not yet covered. “Yes, it’s finished, too,” the expert notes of the astonished looks. “We set ourselves the goal of achieving a higher quality that would remain visible afterwards. So no suspended ceilings. We also want to show our visitors these solutions later.”
However, the Stuttgart-based company wanted to break up this rigid practice and implement a much more agile form of building planning and construction. Together with the Swabian Würth Group, Drees & Sommer developed another revolutionary concept.
Thomas Berner describes the process: “We wanted to achieve the highest possible level of prefabrication. Together with Würth, we developed TGA modules. These are five-meter-long modules that contain elements of the technical building equipment, such as heating, air conditioning and electrical engineering. The modules can be manufactured in the hall, regardless of the weather or location. They are then delivered to the construction site by truck just in time and assembled here. And only one team is needed. This reduces the workload of the fitters and at the same time increases quality, as the individual modules can be produced with millimeter precision. We are also much faster, completing in half a week what would otherwise take two weeks. On the third floor, for example, it took four hours to complete a 400-square-meter unit. Heating, ventilation, plumbing, refrigeration and electrical wiring, fully insulated and with all valves mounted so that the strings can be pulled separately.” You can clearly see the old hand’s enthusiasm.
Late, but successful
So it’s all sunshine and roses when it comes to the new building? Steffen Szeidl admits: “Nevertheless, we almost made a crucial mistake. We didn’t get Phoenix Contact on board until relatively late.” The expert describes the usual practice: “The I&C, i.e. the building automation, usually gets the contract last in the construction process and then has to put up with what the other trades have defined in their tender. In this way, building automation, which actually stands for efficient integration of the trades, often remains a patchwork. Far too late, it has to knit a coherent overall concept out of many preliminary services provided by other trades, trapped in the most diverse interfaces, different functionalities and great time and cost pressure.”
However, since Phoenix Contact and Drees & Sommer were in close contact in other projects, the topic of OWP12 came up at some point. Just in time, as Szeidl emphasizes today: “I am very glad that Phoenix Contact joined us in the late planning phase. Because the East Westphalians brought the topic of IoT-based building automation into their concept of smart building design as a decisive impulse in this phase.
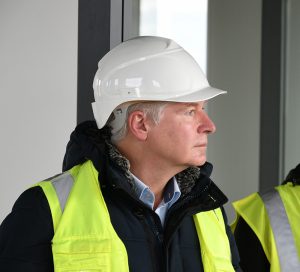
Bernhard Tillmanns, Director Industry Management Building Technology responsible for the topic at Phoenix Contact, adds: “We recommended the company BIT as our system partner for the project. BIT comes from a data center construction background, with expertise in utility engineering. These experts also brought IT expertise, data modeling and IT security to the construction phase, skills that are necessary in the construction of an innovative building management system. It was very important to us to change the mindset here. Only if this expertise is integrated early on can a building also develop completely new capabilities later in operation.”
Hardware is just the shell
Steffen Szeidl adds: “Planning, construction management, completion date and operation – these are often separate ways of thinking and different tasks. With OWP12, on the other hand, we had everything in one hand. And we want to take advantage of this opportunity. We no longer just talk about hardware that I can touch. Is the door mounted correctly? Have the cables for fire protection been pulled out?
In the past, the software share in a building was very manageable. In our projects ‘The Ship‘ in Cologne, ‘Hammerbrooklyn‘ in Hamburg or the ‘Cube‘ in Berlin, we have therefore worked with our customers to anchor a digitization strategy that enables new business models. If I rent out my offices by the hour, for example, and this is done via an app through which the customers book and also receive the invoice, then this has to work. And if the software doesn’t work, along with all the technical functionalities behind it, then the whole business idea I have for the building could be overturned. So it’s no longer just important that the hardware gets done. The focus is also on the software, which enables new business models.”
In OWP12, a specially developed app is used to make all room and office space bookings, among other things. Drees & Sommer has been working without fixed workstations for several years. In addition to this tool, there is access control with the app. The cafeteria also works with recording and billing in the app.
Thomas Berner tells us that developing your own app is now as much a part of a modern office building as ventilation or heating. “It’s no longer just a matter of the physical building being ready on time. Additional time has to be scheduled so that the necessary software can also be tested in operation. This is changing the way we think about construction.
And if we only work on one software platform, i.e. avoid subsystems from a whole host of individual trades, then we are in a much better position to deal with crisis situations, for example. At any point where I need that as an operator, I can later determine where I need switches, for example, because the structures allow that. And that’s where the Emalytics functionality from Phoenix Contact scores decisively.”
Steffen Szeidl agrees with him: “In the future, we have to think about building automation much earlier, already in the planning stage and much more fundamentally. This is the only right way, and we will also be repositioning it internally in future projects. The adaptation possibilities of Emalytics into the future are simply convincing. And with the Phoenix Contact system, we are completely flexible and can reallocate uses without having to lay completely new cable routes. We can use software programming to change things without anyone even noticing, without any structural measures. This is what building of the future must look like.”
Drees & Sommer
YouTube: The green facade of OWP12
YouTube: Prefabrication TGA modules
Phoenix Contact Building Automation
Whitepaper zum Thema Smart Building Design