He was one of the attractions at the 2019 Wind Power Technology Congress in Blomberg: Jörg Spitzner fascinated the audience with his vision of a wind turbine generator that not only generates electricity, but also fishes CO2 out of the air.
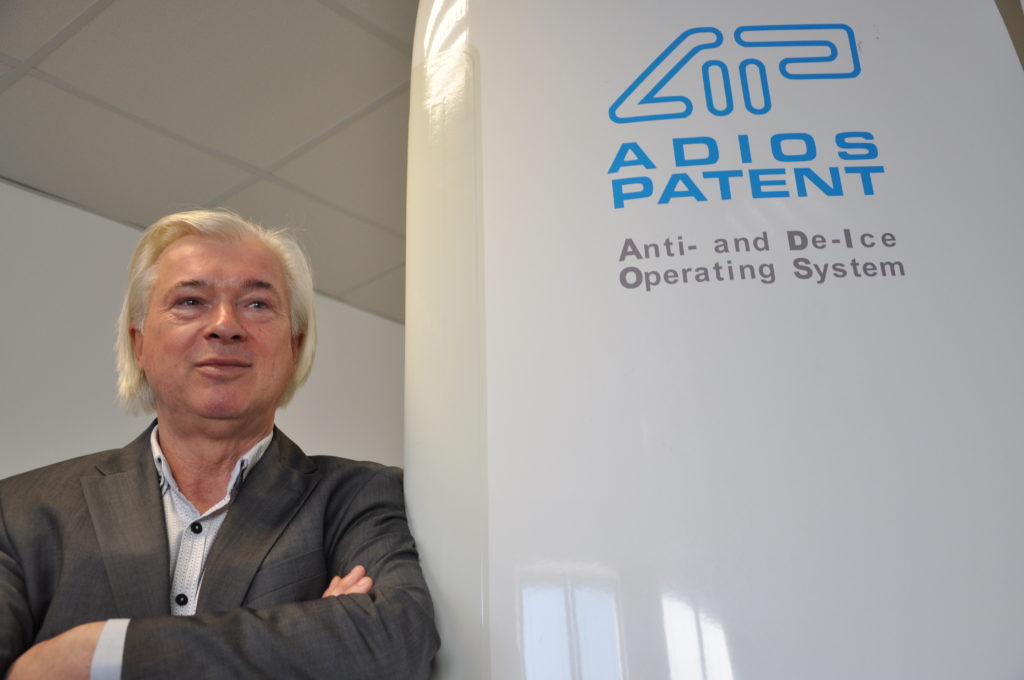
In February 2019, an exquisite group of wind power experts met in Blomberg for the third annual Phoenix Contact Wind Power Technology Congress. Exciting topics attracted visitors to the Blomberg auditorium – from ice detection to additive manufacturing, the use of Proficloud and the revolutionary PLCnext Technology to sophisticated vibration analysis of wind turbines to avoid night shutdowns.
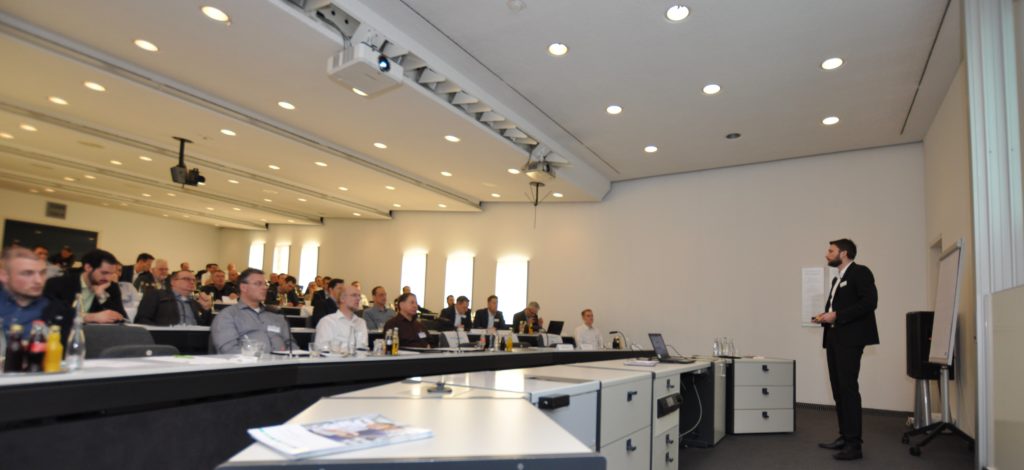
However, one presentation was so visionary that the author of these lines decided, after consulting with his colleagues (“is he crazy or is this to be taken seriously?”), to revisit the topic of “Blancair” and the CO2 vacuum cleaner on the wind turbine generator in a direct conversation on site in Hamburg Finkenwerder.
Preisgekrönter Unruhegeist
If someone were to award the title of Daniel Gyro Gearloose, then Jörg Spitzner would certainly be at the top of the list. And quite literally, because the engineer and mastermind behind Spitzner Engineering really knows his way around engines, jets and aerodynamics. After all, Spitzner worked for many years in research and development at aircraft manufacturer Airbus.
But at some point, the busy free spirit found the corporate corset too tight – he founded his own engineering office, Spitzner Engineers, in 2007. What began as a team of three now has a proud 40 employees. His main customer is his old employer Airbus, which is based just around the corner here in Hamburg Finkenwerder.
From the wing to the blade
But you can’t stand well on just one leg. Jörg Spitzner and his team are experienced aerodynamicists. It’s not far from the wing of an Airbus to the rotor blades of a wind turbine. Spitzner took the plunge. And with success: “Since then, we have been transferring aircraft construction technology to the wind industry,” explains the 56-year-old engineer.
In 2009, Spitzner Engineers developed the principle of influencing the flow on the rotor blade: “We open the tip of the rotor blade and ensure aerodynamic optimization by drilling small holes at the root of the blade. The rotational energy alone creates an air flow that significantly increases the energy yield of the modified wind turbine generator.” As part of the project, they also provided the rotor blades with winglets and a sawtooth-like trailing edge: “The boundary layer influence is known from aircraft construction and is known to work very well there.”
Spitzner then found an expert partner in Phoenix Contact for the next development, an innovative de-icing system for the rotor blades. “The idea, calculations and commissioning came from us. But we are not electronics engineers, that was done by our colleagues at Phoenix Contact.” The “Anti- and De-Ice Operating System” (ADIOS) is now almost ready for series production and the first test systems with the electrically heatable coating have been set up.
The CO2 vacuum cleaner
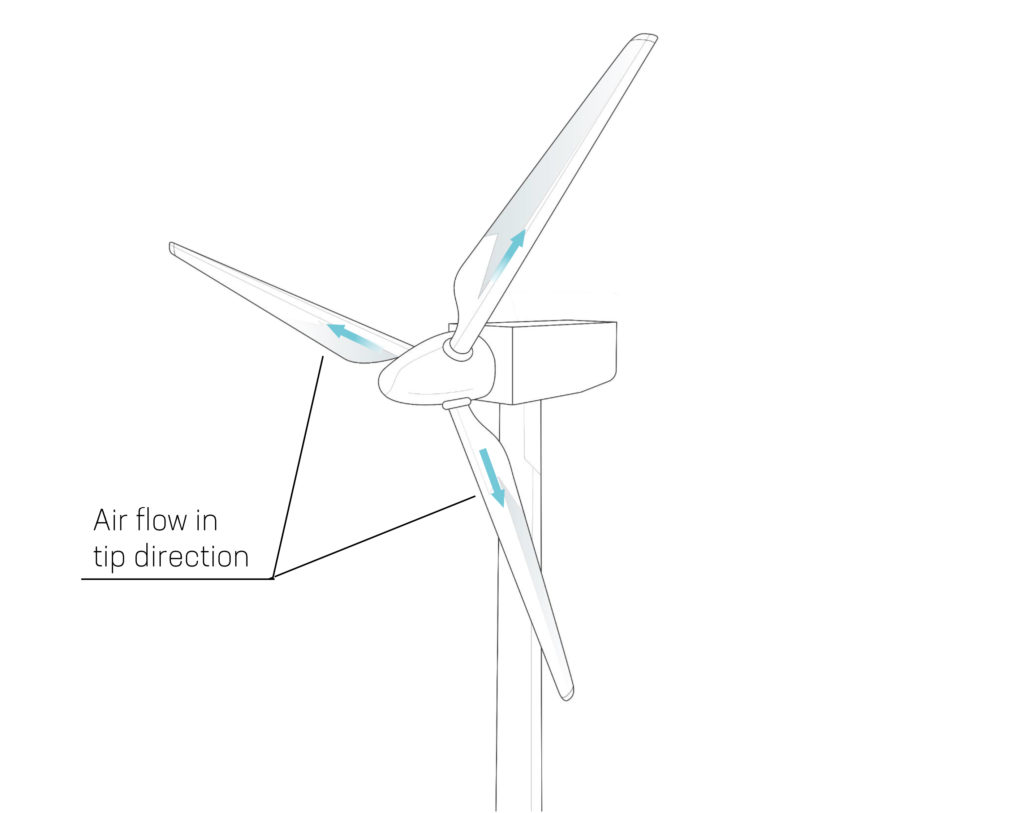
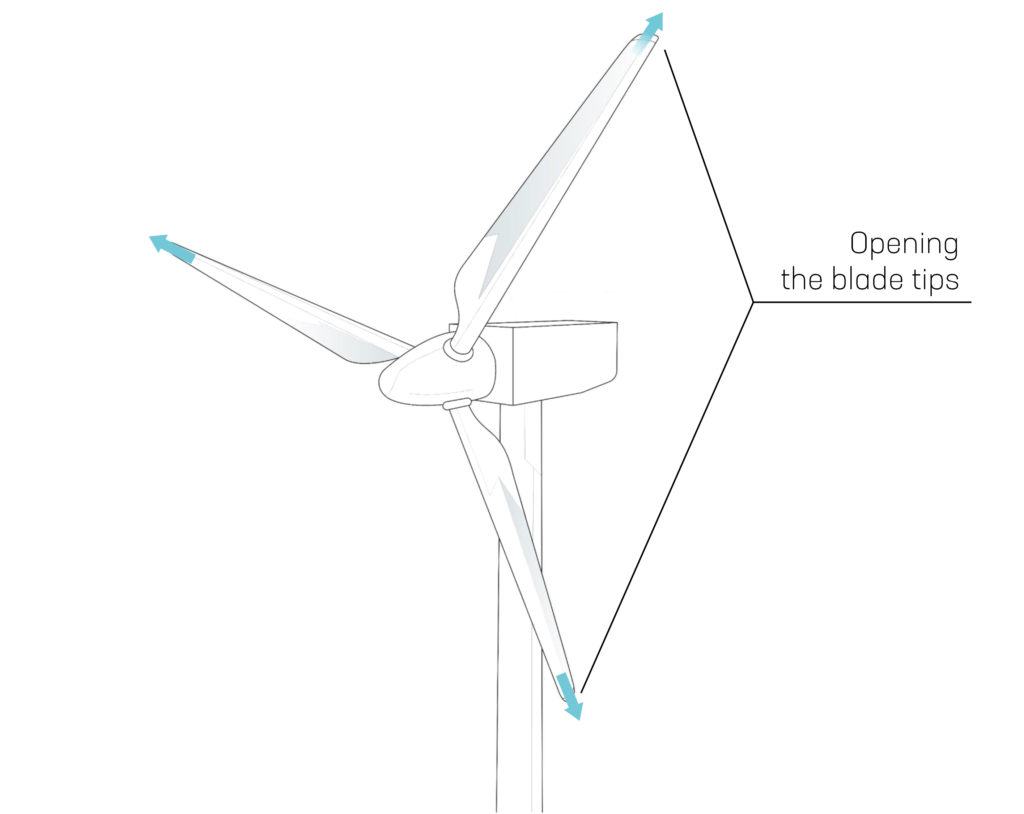
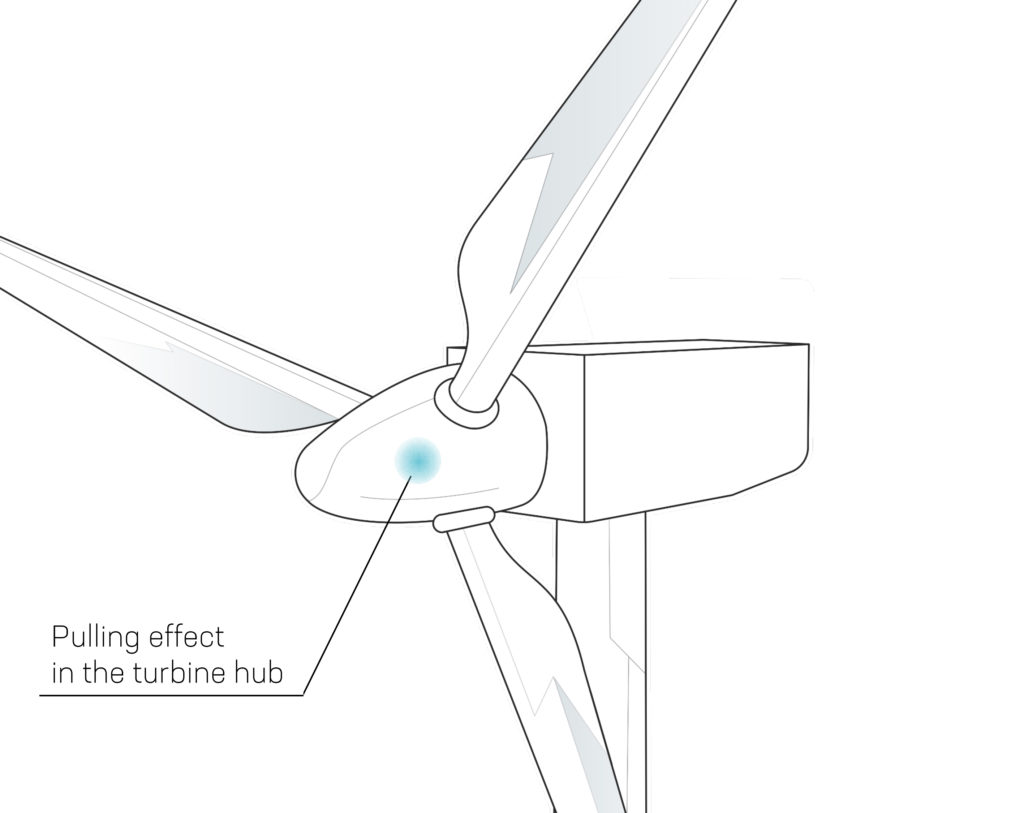
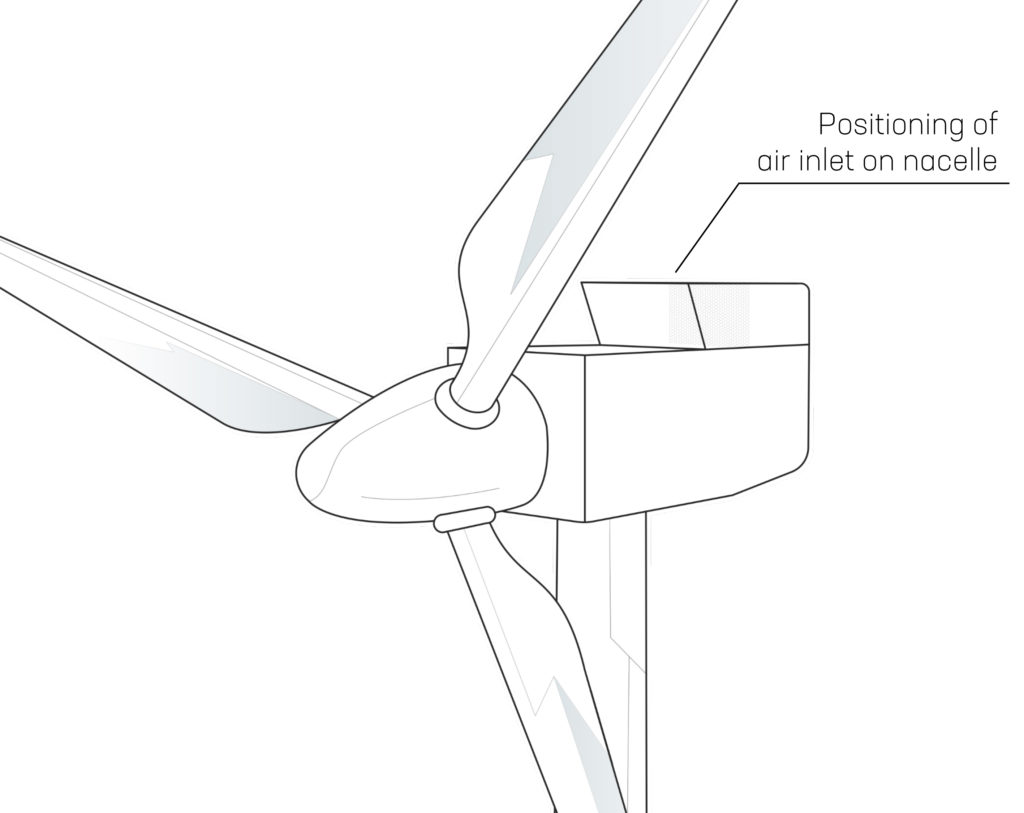
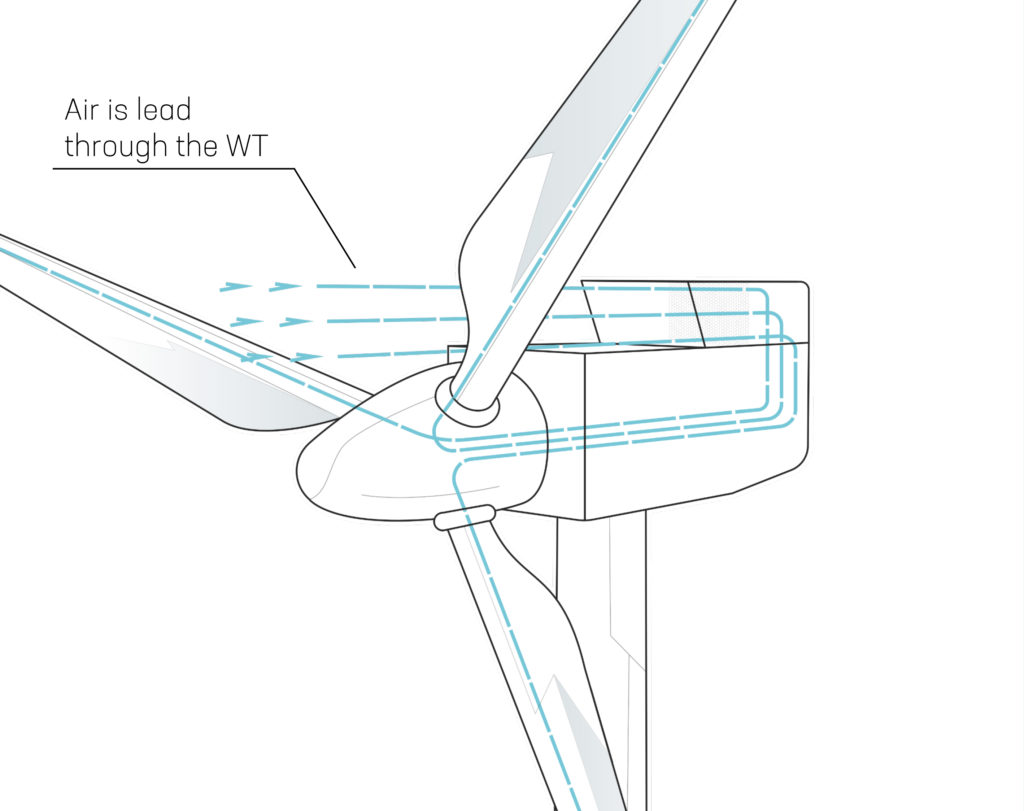

The latest trick in wind power is based on the experience gained from rotor blade optimization. “When you open the blade tips, the initially stationary air flows outwards as it moves – just normal centrifugal force (Figures 1 and 2). The force is enormous. We then looked at what actually happens if you open the root towards the hub of the wind turbine (3). And we came to the conclusion that the circulation that now occurs would be ideal for drying the air (4). Condensation is a huge problem, especially in the offshore sector – just think of the corrosion.”
But Spitzner and his colleagues thought one important step further: “If the air flow generates such energy, then we could actually filter it as well (5). This provides additional drying in the system. And – here comes our clean energy one approach – we could filter CO2 out of the air.”
CO2 filtration is not new. The approach: despite all climate protection measures, far too much CO2 will continue to be blown into the atmosphere worldwide for many years to come. Active removal is therefore urgently needed. “And that’s exactly where we started. By opening the rotor blade tips, we have so much energy available that we can suck in air and filter it. We can separate and collect the CO2 in the process (6). And make it processable all the way to eFuel – or store it.”
It pays off!
Jörg Spitzner may be a visionary, but he is no fantasist: “Of course, we also asked ourselves at the beginning whether this could work at all. How should such a retrofittable system be dimensioned? Would it even fit into a wind turbine nacelle? How expensive will such a system be, will it pay off?” Today Spitzner is certain: “It pays off. The idea is really disruptive. And it’s now also patented.”
When asked whether he sees himself more as an engineer or a climate climate saver, Spitzner has to smile: “Both fit. With us mainly come up with ingenious ideas. But we also have a social responsibility. We also want to subject our expertise to ethical standards. to ethical standards. For example, we refuse to accept any orders from the arms industry.”
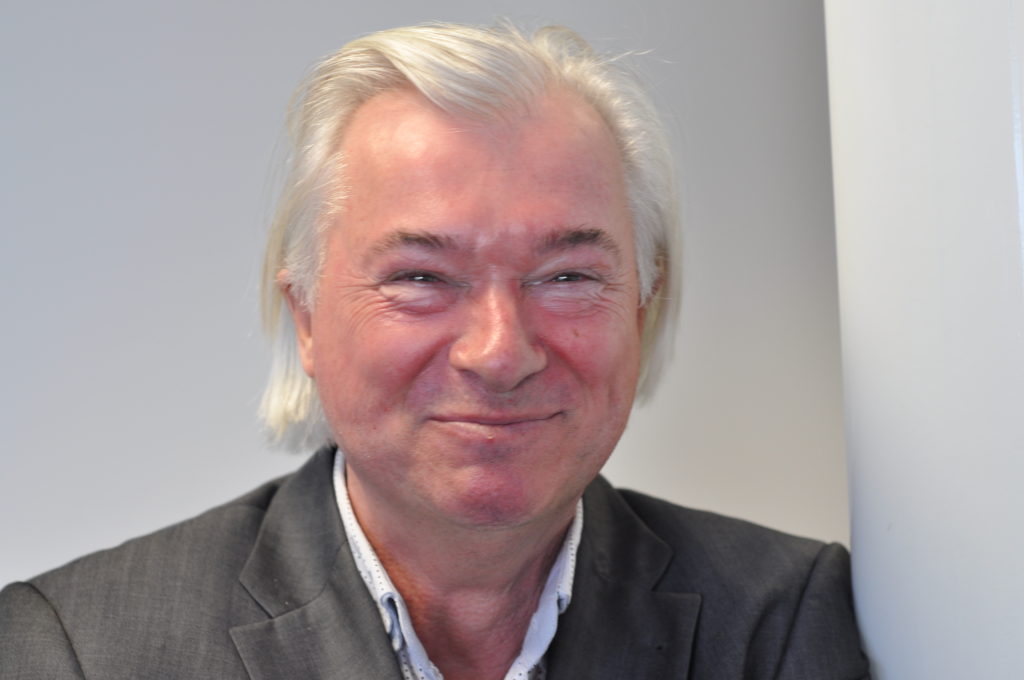
Anyone who meets Jörg Spitzner will suspect that he and his team have by no means reached the end of their innovative power. One or two ideas are certainly already waiting to be presented – perhaps at the Wind Power Technology Congress 2020 in Blomberg!