Anyone who wants to teach wind turbine generators their power-generating manners has to go right to the top from time to time to install or check that everything is in order. An adventurous job that requires special training.
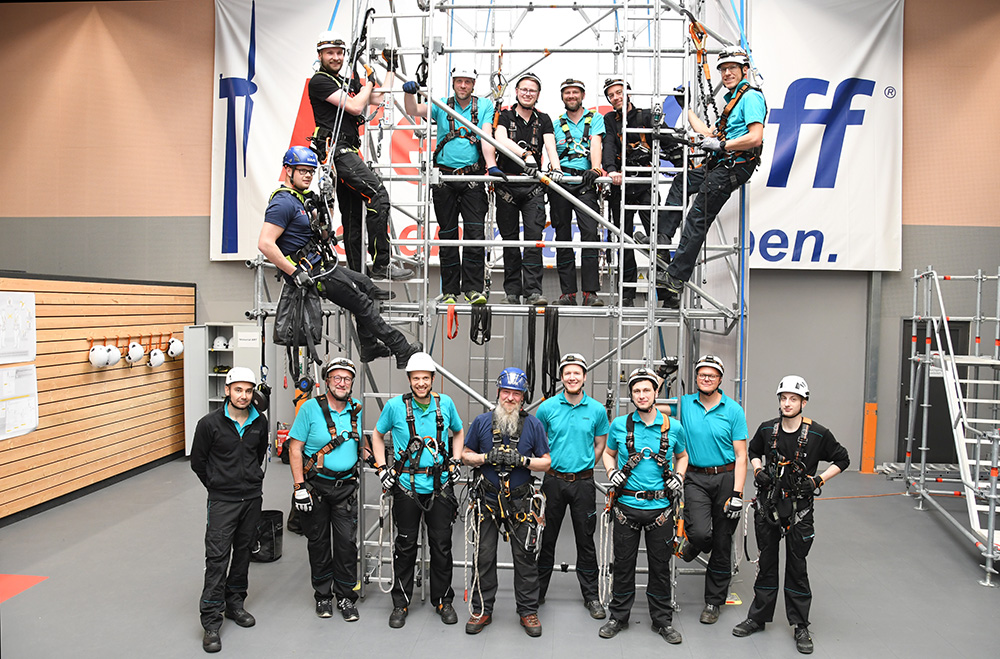
If you want to get to the top, you have to start at the bottom. In this case really at the bottom. Lukas Christ lies on the asphalt, his head bandaged. A shiny thermal blanket is protecting him from the cold and hypothermia. In the background is a battered car, in front of him a first-aid kit. We are in Bissendorf near Osnabrück, at the depot of Rescoff. And Lukas Christ uses his technical expertise to look after Phoenix Contact’s major customer Enercon when he’s not playing the accident victim.
The Phoenix Contact wind team is almost complete for the annual safety training course. Whether salesperson or technician, engineer or Manager – when it comes to safety on the wind turbine, everyone is the same: the thirteen participants are armed with safety shoes, climbing equipment, helmets and robust clothing. “There are usually two of us on a turbine. And if something really happens, there’s only one colleague up there who can help. You have to be able to rely on each other,” explains Nils Lesmann, Business Development Manager in “civilian life”.
School desk before action
But before they go up into the air, basic knowledge and theory are on the agenda. Even if the professionals have heard it many times before: What is a technical installation? How do you make it safe? How do you behave in the event of accidents on and around a wind turbine generator?
What accidents are possible? The German Social Accident Insurance (DGUV) distinguishes between three danger zones: The mechanical hazard from sharp edges, unprotected machine parts or the freight elevators. A wind nacelle is not an apartment, even if the dimensions of large turbines would now exceed those of a tiny house. The electrical hazard of the “closed electrical operating facility” is obvious, which is why only persons who are trained as electrically skilled persons are permitted to work in these areas. And finally, not everything in a wind nacelle or tower is harmless to health. Epoxy resins, lubricating and hydraulic oils or cleaning agents require careful handling and appropriate contactor protection.
And sometimes the engineer or service employee carries the risk with them. After all, a stroke, heat shock or a heart attack are also life-threatening situations in the seclusion of a wind nacelle. The obligatory examination by the company doctor, which is required every three years, is therefore routine for the members of the wind team. In addition to an ECG, blood and lung tests are carried out to check whether the employee is fit to work at height.
Stress in the labyrinth
In the meantime, Lukas Christ has been “rescued”, his colleagues have routinely set the rescue chain in motion and treated the “casualty”. The two instructors increase the stress level: now the “injured” are to be rescued from a wire box maze, which is intended to simulate the confines of a wind turbine generator. Hoses block the way, boxes are additional obstacles. Sometimes it’s a heart attack that needs to be treated, sometimes it’s a fracture that needs to be splinted in the confined space before it can be removed.
Björn Bülter now works in sales as a key account manager for the German wind turbine manufacturer Enercon. Before he started at Phoenix Contact, he was a service technician himself and worked on a number of wind turbines: “It’s very realistic here. Up on the real turbine, the route often leads us from the nacelle via narrow paths into the front hub, past all kinds of equipment and underneath in crawl space. And if we want to install and calibrate sensors in the blades, for example, we have to go even deeper into the system and it gets even narrower.”
Things are looking up
The second day – it’s time to climb. But before the climbing harness is put on and the helmet strapped on, an experienced instructor gives another theoretical introduction to the subject. Material science is the order of the day. It’s about equipment that you probably won’t find anywhere else at Phoenix Contact: Climbing harnesses and harnesses, carabiners and pitons. This part of the course is called “Working at Heights”. “On my first courses, we actually went down from an 80-meter tower afterwards,” says Karl-Heinz Meiners with a grin. The 53-year-old Senior Project Manager is a veteran of the team and has worked on wind turbines in a number of countries around the world. Today, the eight-meter-high tower in the Rescoff hall is all he needs.
“You have to be fit for this course,” blows Karl-Heinz after getting out of the super-narrow elevator, which barely has room for two people and still needs to be left at the bottom. Not for people with claustrophobia, “and you shouldn’t get dizzy in this job anyway.” But anyone who, like Karl-Heinz Meiners, has climbed wind towers during winter storms in Inner Mongolia 20 years ago, “still without an elevator and with a trouser belt for safety”, remains cool even when faced with such challenges.
“The training here is much more strenuous than any real work on the turbines anyway.” The senior member of the wind team has only been really scared once: “That was a good 20 years ago, on a Chinese turbine. We were up there because of a fault while the turbine was running. Today that is strictly forbidden. And then the turbine went into emergency stop. In other words, the rotor came to a full stop in a flash. There was a huge bang and then we flew through the area. And a lot of sparks were released along with us. And fire is the worst thing that can happen up there. That was the only time I was really scared.”
Out and down
Respect is a must if you want to leave the lofty workplace unscathed. “We’ll soon be in Portugal on a plant where we have to go into the hub. That’s where the control cabinet for the sensors we use to measure the blades is located. The problem is that we have to climb out of the nacelle and then outside in front of the hub, where there is an access door. There’s no way through from the inside,” explains Lukas Christ, who was the casualty of the accident the day before. He tightens the climbing harness with a jerk and then hangs limply: accident victim again! This time he is abseiled down and plays the unconscious man dangling in front of his “rescuer”. However, things are usually much better for the youngster, who joined the team in 2016: “I’m often on Enercon prototype systems, helping with technical acceptance tests.”
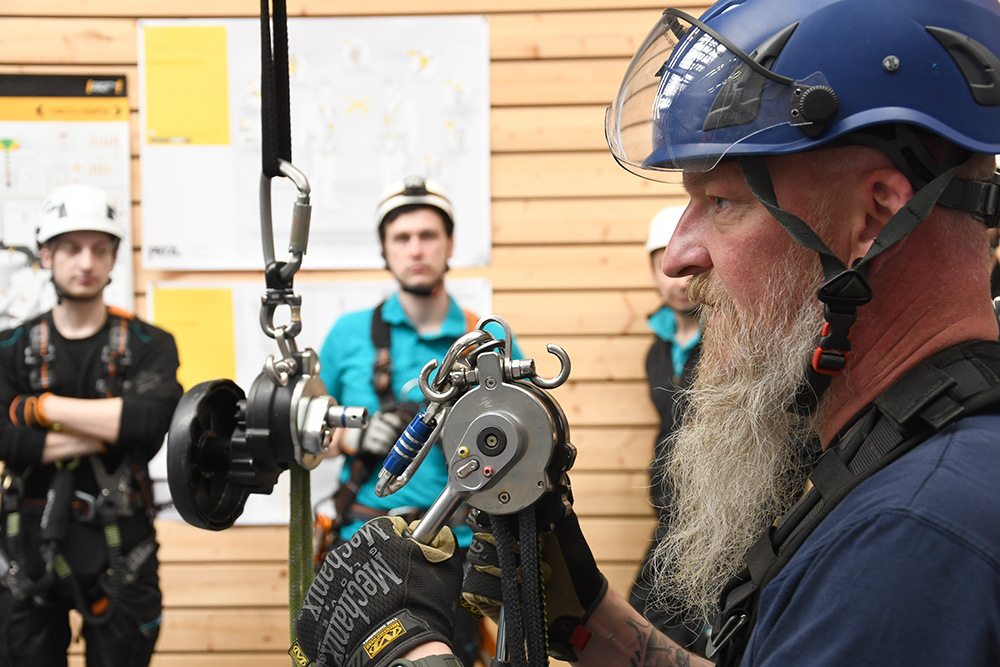
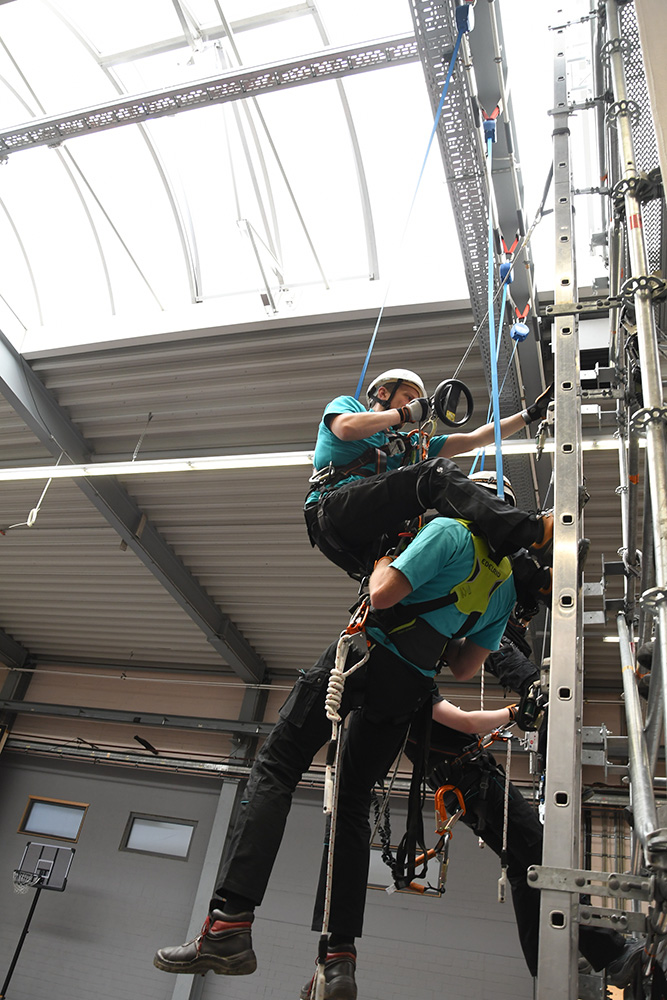
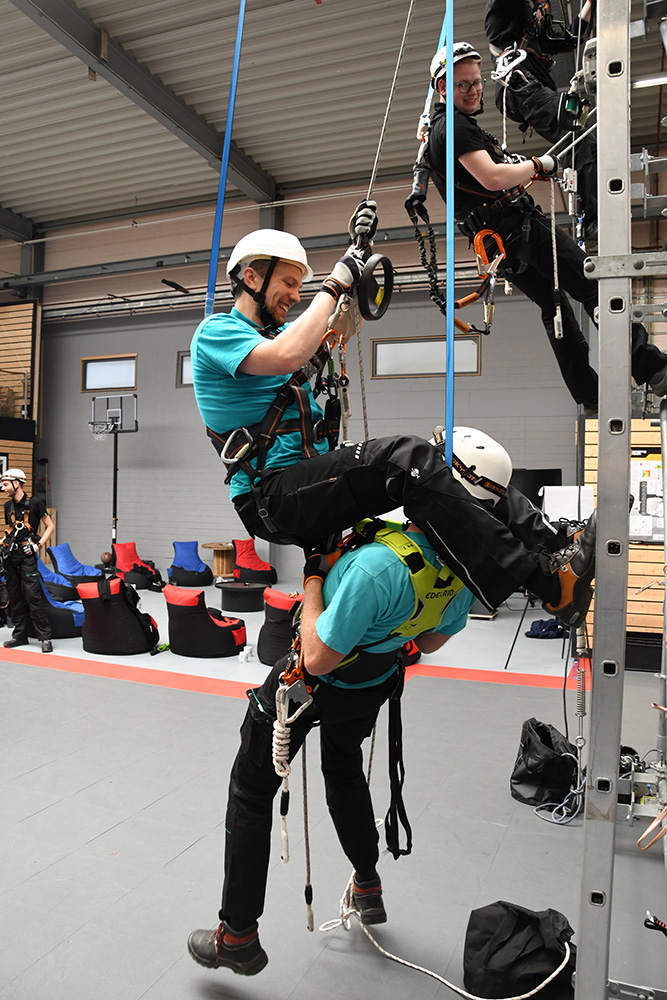
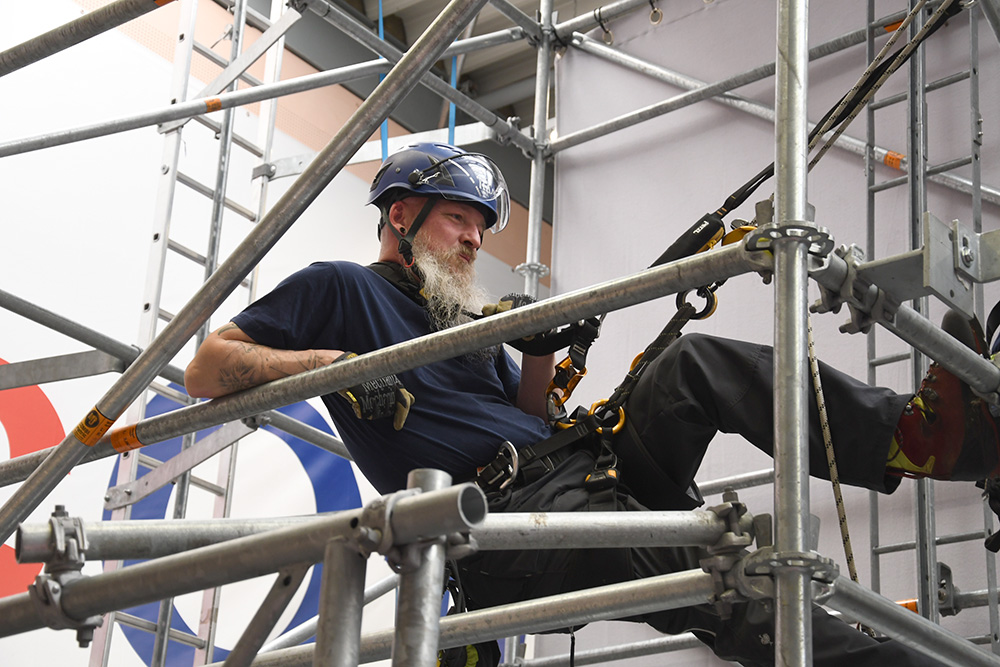
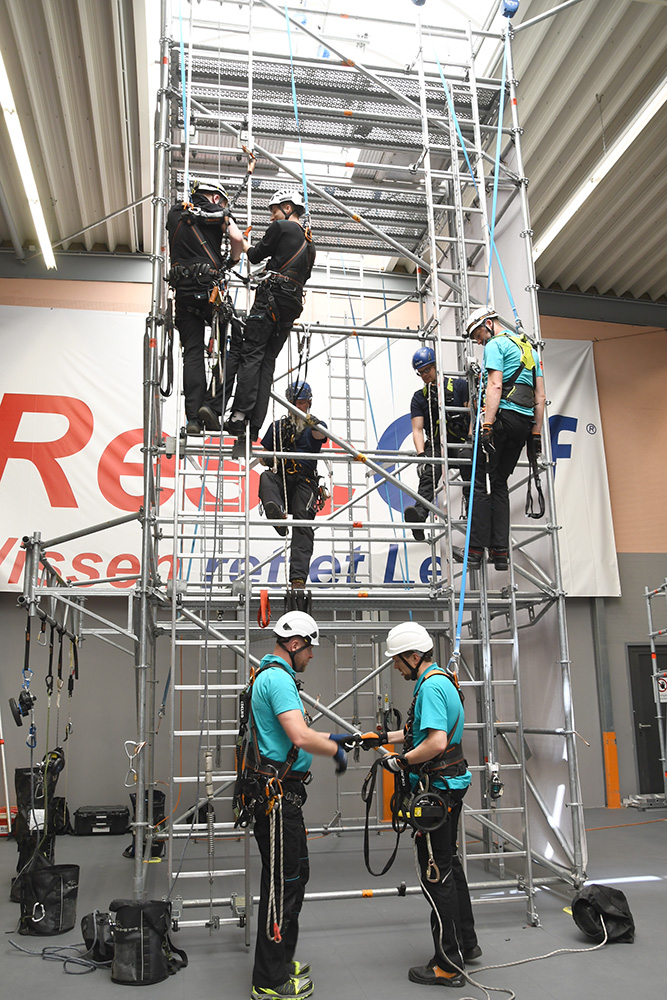
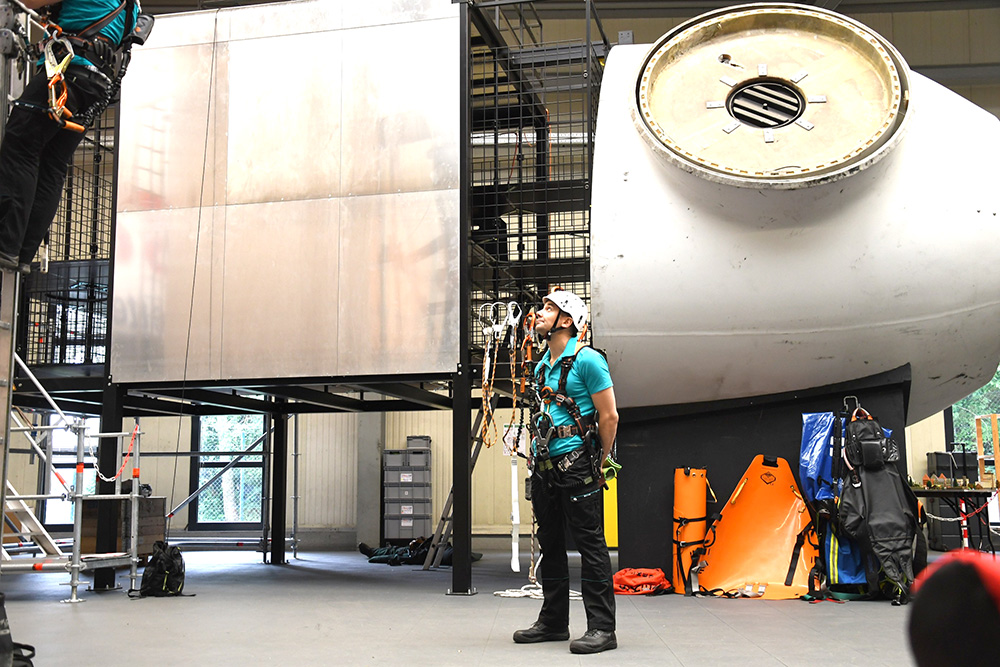
Anyone working on wind turbine generators is largely isolated despite the close proximity and must be able to help themselves or their partner. This is even more the case with offshore wind farms. Björn Bülter: “I was offshore relatively early on, in 1998/99 for the first time. There weren’t many turbines back then, so we had to take part in the training for working on an oil rig. We took the ship out to the North Sea off the Irish coast. Transferring from the boat to the platform was the most dangerous moment of the trip – the ship goes backwards. You have to wait for the exact moment when the wave lifts the boat to the highest point and then over to the ladder and then up. The more waves, the more exciting it gets.”
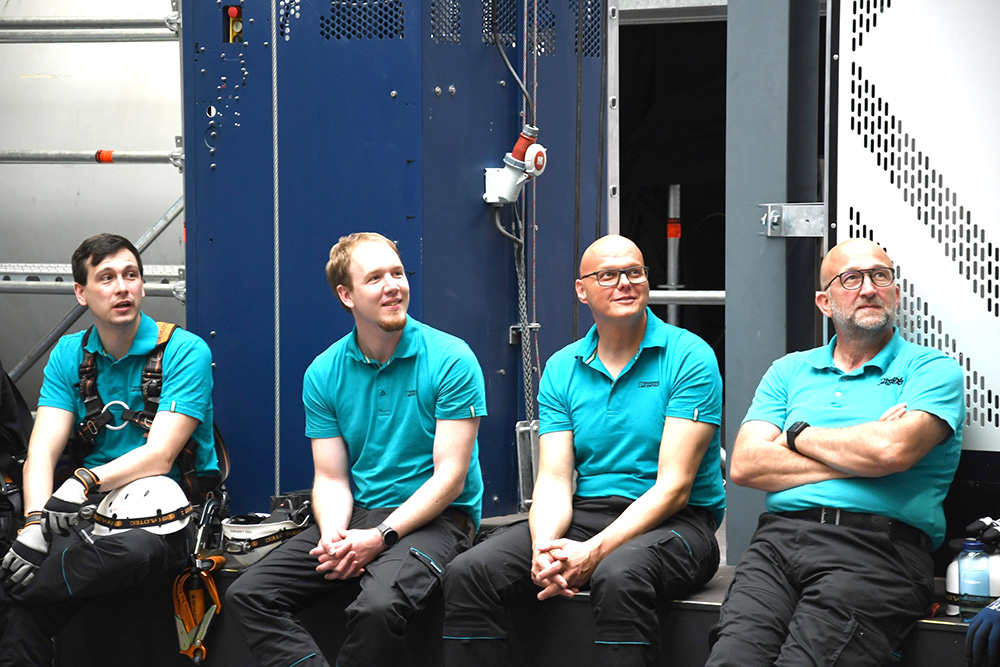
However, thanks to the now mature and globally valid safety standards, serious accidents on and in wind turbine generators have become rare. And regular training is also an important part of ensuring the safety of Phoenix Contact’s specialists. Nevertheless, the job remains a challenge …