The more gentle the bouncer, the more pleasant the entrance. A visit to the Westphalian town of Lippstadt shows why this is not only the case when it comes to admission to sought-after hangouts. ASO Safety Solutions GmbH is located there. And they know how to teach mechanical inlet regulators the right manners.
Closing is part of their job, but project manager Norbert Pewny and hardware developer Dennis Mettner are not at all closed off when it comes to the latest product from their ranks: “With Drico 2.0, we have achieved an unprecedented level of flexibility on the market,” says Pewny, summarizing the advantages of the new gate controller. The two experts work at ASO Safety Solutions in Lippstadt. The company is one of the leading developers, manufacturers, and distributors of security solutions for doors, gates, and machine building. Around 170 employees work here and at locations in the US and China on solutions for conveying technology, lifting and access technology, industrial truck technology, and the safety, sensors, & controls sector.
The gate is a machine
In the latter area, ASO manufactures three large product groups that ensure that moving door and gate elements don’t get out of hand: safety contact strips, safety contact buffers, and safety contact mats. What they all have in common is a control unit that collects the data from the sensors and transmits necessary commands to the system or vehicle controller.
It sounds simple, but it is full of technological challenges when it comes down to the details. Because what is most important is signal acquisition and processing that are reliable and as fast as possible. Who wants a fast-moving roller shutter to turn into a guillotine when it closes? Dennis Mettner shows what’s important for the safety contact strips used here at the bottom edge of the gates: “Contact strips are attached to the flexible rubber elements. If they touch each other, such as when the door meets resistance, the system control switches the drive off at lightning speed, the motor stops, and the door comes to a halt.” Project manager and electrical engineer Norbert Pewny adds: “We look at a gate like a machine. That’s why the same strict safety regulations apply.”
Machine stopper
ASO knows all about this, because their contact mats and bumpers ensure that even machines in operation have the right manners when they come into close contact with their human operators. This becomes clear, for example, in the case of the contact buffers, which are say the bumpers that are attached to the moving portals of large CNC milling machines. These gantries are mounted onto a machine table on which the workpiece, say a wooden plate, is fixed. The tools for machining are mounted on the portal, moving on rails. Controlled by a machining program, the portal moves in such a way that the moving tools, such as drills or milling machines, can be activated at the right places on the plate.
If an operator now gets in the way of the heavy gantry, accidents could happen. However, large-area barriers would get in the way of the space required by a production facility or workshop. But by using bumpers, the controller reacts with lightning speed to unplanned contact and stops the heavy machine.
Domestic production
When walking through production, it’s surprising to notice that ASO manufactures most of the elements itself. Long conveyor lines run through production; the rubber elements are also produced here, and their development is precisely controlled.
“Our vertical range of manufacturing is one of our arguments that wins us customers,” reports Mettner. “It is precisely this that allows us to respond individually to every customer request. Our customers are mainly from industry and the manufacturing sector, where custom-made products are quite commonplace.”
It is precisely this flexibility that is also the focus of the exchange between the two experts and the Phoenix Contact experts. The gate controls are available in different performance classes with correspondingly scaled functional equipment. “The upper performance range we offer includes gates that are used very frequently, such as those with several drives, induction loops for control when starting up conveyor vehicles, or with our own signal light system,” explains Pewny. “The more complex the overall system is, the more important safety-related functions become. The functionality of the controller must keep pace accordingly.
480
Gate control variants are possible with the SKEDD direct connectors.
The basic idea behind developing the new control system was to achieve the most transparent hardware scaling possible, the benefits of which our customers can immediately understand.” The respective hardware equipment carries out central functions of horizontally or vertically opening gates, depending on the features. These include controlling frequency converters and three-phase motors to open and close the gates, safety functions such as photoelectric barriers or dead man’s switches, and additional features such as thermal switches, wireless receivers, position encoders, or LC displays. And of course, this area also includes possible electronic access control in numerous variants.
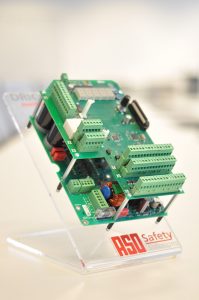
Gentle thanks to the module option
The more sensors a gate controller has, the more sensitively it reacts to signals from the operator. Mettner and his development team use SKEDD direct connectors from Phoenix Contact to connect the drive-relevant functions. The modular system includes a total of nine different PCB layouts, enabling developers to scale the scope of functions of their gate controller precisely. Hundreds of combinations are possible, which the automated doormen from Lippstadt are supposed to make more and more precise. The more gentle the entrance, more secure and comfortable the user feels.