How are you supposed to access the data generated by a bearing that is located in a gigantic mixing tank in which hot molten plastic is sloshing around? A research group from TU Dresden, in cooperation with BASF and Phoenix Contact, are working on precisely this issue.
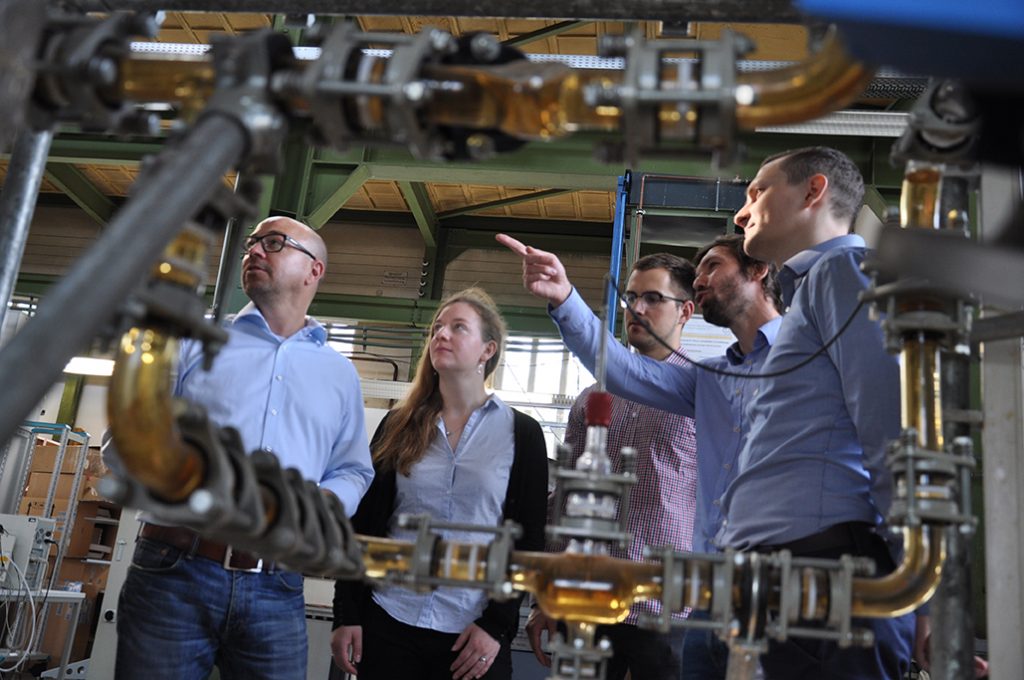
The BASF facility in Schwarzheide, Germany, produces chemical base materials. Located in the middle of the lignite mining area of Lusatia, the plant was established in 1935 as the Schwarzheide Hydrogenation Plant, and was initially used to produce synthetic gasoline from lignite. Today, it belongs to BASF SE and its main purpose since 1972 has been polyurethane production. In addition, the plant also produces engineering plastics, foams, pesticides, and paints.
Avoiding downtime at all costs
Processes such as heating, cooling, mixing, and casting are used to synthesize the respective end products from the base substances. The contents are mixed together and heated to temperatures of several hundred degrees in powerful mixing tanks. These are a central component of the production process. If the tanks stop, production stops. Then it gets expensive.
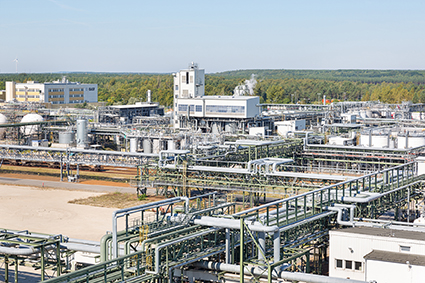
The mixer units in these tanks are moved by extremely strong bearings. These bearings are subject to normal levels of wear. The problem is that, because the mixer units are in the tank, the bearings are inaccessible. If the bearing fails, it happens suddenly and without warning. Therefore, maintenance routines in which the mixing tank can be inspected and, if necessary, the bearing replaced must follow a rigid schedule, which is always shorter than the actual wear, so that the system can be shut down in a controlled manner.
Wouldn’t it be nice to be able to determine the state of the bearing and therefore the stability of the process more precisely and as close to real time as possible? Then production would only have to be stopped when the state of the bearing actually necessitates a replacement.
But how do you access the bearing? And which sensors can withstand exposure to aggressive chemicals under heat and pressure reliably and for years?
Project wanted
This is where the new PLCnext Technology from Phoenix Contact comes in: this open-system control technology uses high-level languages. And not only that – state-of-the-art software tools such as Matlab Simulink are easy to integrate into PLCnext. This needed to be proved. So, as part of this year’s NAMUR Annual General Meeting, attendees set out to find a project in which PLCnext Technology was confronted with monitoring slow rotating equipment – a typical application in the
process industry.
That’s when TU Dresden came into play: after all, Head of the Chair of Process Control Systems and the System Process Engineering working group at the Technical University Dresden, Professor. Dr. Leon Urbas, knows the industry. And he knows Phoenix Contact. He gave the right advice regarding the hot tank and its battered but almost inaccessible bearing.
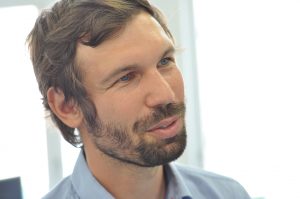
Dr. Markus Graube is the head scientist in the “Process To Order” laboratory at the institute. This laboratory is considered a leader in Germany when it comes to “model-based, data-driven, and information technology approaches for describing and predicting the behavior of modular systems”. Simply put, scientists want to use data to make predictions about the state of systems. This is to say, to be able to look into the tank without having to physically access it.
This makes them ideal partners for PLCnext Technology. The students use high-level languages to program the algorithms with which the controllers can make predictions based on the data obtained and derive actions such as alarms or the reduction of rotational speeds. Programming in machine code, which classic controllers work with, is too complex and expensive.
Talking shop at the switch cabinet Working on and with PLCnext The control “understands” higher-level language The researchers are using algorithms to develop For this they use Matlab Simulink TU Dresden focuses on practical experience Another project, just as fascinating – an algae reactor
Ideal partners
In cooperation with the specialists from Phoenix Contact, Graube and his team developed a complex algorithm that makes it possible to draw conclusions on the state of the bearing from the current consumed by the electric motor, the temperature, and the composition of the material in the tank.
The algorithm, created with the help of Matlab Simulink, is able to recognize any deviations caused by a defective, sluggish bearing and to issue a warning before the bearing completely fails. The algorithm was uploaded to the controller without any problems.
In order to enable the target predictive maintenance, the control cabinet and its innovative controller are now installed on site and are busy recording data. The bearing, however, is not yet playing ball. So far it has run smoothly and there have been no situations in which intervention was necessary, which would allow the algorithm to learn. Everyone involved, however, is in full agreement: it’s only a matter of time.