Ferris wheels have been the attraction of every fair for centuries. The round gondolas tower high above every fairground and most houses. But behind the colorful façade, state-of-the-art technology ensures the necessary safety for an entertaining excursion to lofty heights.
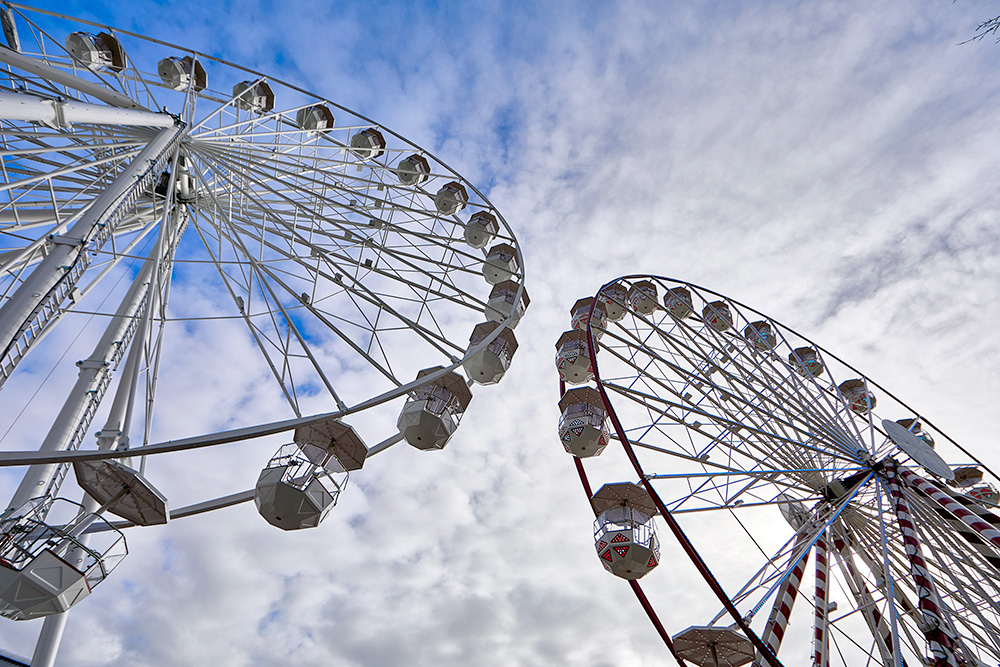
Generally speaking, Ferris wheels are divided into stationary and mobile installations. According to Wikipedia, the oldest idea of a Ferris wheel comes from Bulgaria, where as early as 1620 some children mounted seats on a wooden wheel they had set up. The structure worked hand-driven, of course. And in fact still delights visitors and admirers in remote regions of the world today in an almost unchanged design.
Muscle power and e-motor
The first modern Ferris wheel was then presented at the 1893 World’s Fair in Chicago. Called the Ferris Wheel after its inventor, the structure was a remarkable 80.5 meters high. And it was a complete success.
The fascination for the Ferris wheel was awakened. As stationary installations, they still frequently characterize the image of cities today, for example in London or in Vienna at the “Prater”, where the oldest of all active Ferris wheels is located. Or they fascinate in the form of mobile installations at fairs worldwide. In developing countries, Ferris wheels are often powered by muscle power, as there is no electricity supply. But the usual method is to drive them by means of electric motors located to the right and left of the entrance area. Friction wheels are used to transmit the power to the wheel.
The fascination for the visitor lies not only in the unusual perspective from a lofty height. But always also in the slight creepiness, whether the machine really works safely and neither stops nor the gondola crashes. Everything completely impossible? Accidents with Ferris wheels are by no means just an invention from Hollywood action flicks. In 2016, two gondolas became entangled in each other in Nashville/USA, three girls fell into the depths, but survived. In 2013, a gondola crashed from a height of 30 meters in Argentina, killing two sisters. In 2019, a man in Erlangen falls 25 meters and dies. And in November 2021, a Ferris wheel in Cottbus comes to a standstill. Two passengers have to be rescued from a height of 30 meters using aerial ladders.
From carnies to manufacturer
Even though Ferris wheels are actually quite a comfortable form of movement, the safety of the installation is always closely monitored. The Lamberink-Kroon family knows its aerial giants very well. The Dutch company was founded by a family of showmen who had been operating mobile Ferris wheels themselves for decades until 2014, when they began to design and build the rides themselves.
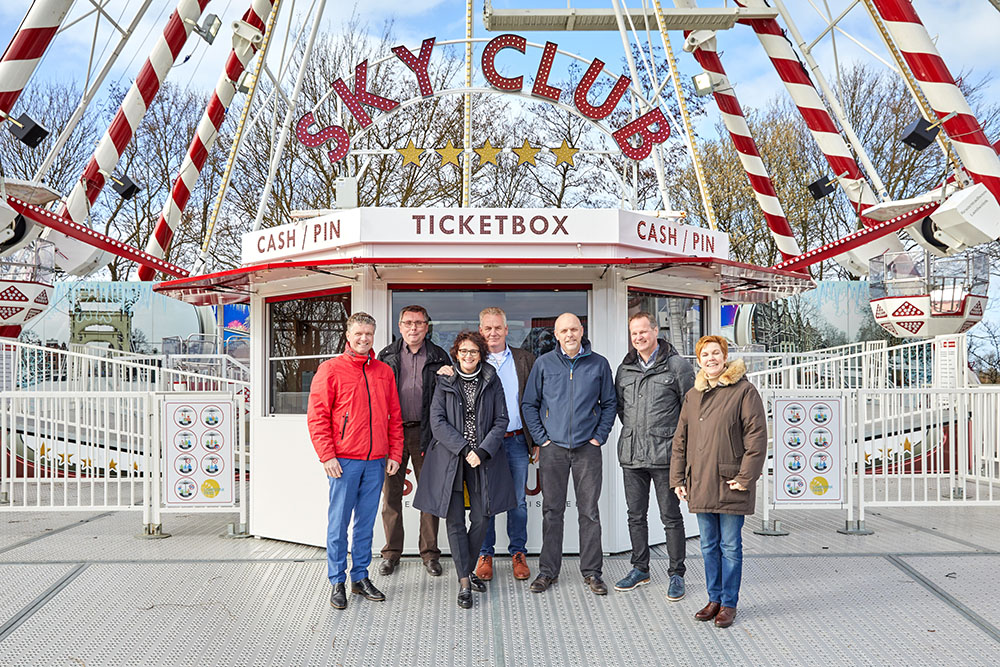
Kokkie Kroon and Jan Lamberink are the bosses of Lamberink Ferris Wheel. It all started when Kokkie Kroon’s father bought a Ferris wheel in 1976. At first, the family of showmen traveled with it from fair to fair. And anyone who travels with such colossi has to deal intensively with the construction during assembly and dismantling. Jan Lamberink soon became interested in building the attractions himself. Since the 1980s, he has been involved in their construction. And he did so in the very company that had manufactured the first Ferris wheel for the family. When this company withdrew from the market, the entire family decided in 2014 to build Ferris wheels on their own. As experienced showmen, Lamberink and Kroon naturally knew and still know exactly what their customers want.
In the meantime, their Ferris wheels have become a household name among showmen internationally. The family has built more than 20 Ferris wheels since 2014 and sold them all over the world. And of course also maintained them, sometimes on site, sometimes on the company’s own premises.
Giant wheel – giant effort
Easy transport, quick assembly and disassembly, low manpower requirements for erection – all important requirements for Ferris wheels. But what does it look like when a Ferris wheel is transported “simply” and erected “quickly”? The 33 meter high Ferris wheel “RL33” requires four trucks for its transport and ten hours each for erection and dismantling. 24 gondolas each hold six people, so that up to 1,150 passengers per hour can enjoy the view.
The “RL46” takes up to 1,800 people per hour to a lofty height of 46 meters. Twelve trucks and two full days each for assembly and dismantling are needed to get the mobile monster into operation.
Amazing figures that make it clear that operating a Ferris wheel is anything but trivial. Intelligent automation technology ensures that when passengers board the gondolas, the load on the wheel is even and the ride time is fair for the passengers. After all, every passenger wants to spend the same number of laps on the Ferris wheel as all the other guests for their money. And also get off the airy funmobile in one piece.
The steel construction of the mobile Ferris wheels is carried out externally on behalf of the internationally active company. For the control cabinet construction, Lamberink and Kroon call on the expertise of the specialists from JB Besturingstechniek in Oosterwolde. Assembly and subsequent commissioning will take place at the company’s site in Overschild. Rides that have already been delivered are also set up here for maintenance and overhauled. In addition to sales, showmen can also rent Ferris wheels from Holland.
What they all have in common is that everything that needs to be electrically connected is extremely robustly designed with connectors made in East Westphalia. And if you think of a Ferris wheel at night, you can guess how many electrical connections are needed to make it a shining landmark of a fairground.
Safety through automation
For the safety of the passengers, it is important that the Ferris wheel does not start moving until all persons are safely seated in the locked gondolas. The operator can monitor the loading of the Ferris wheel via a web-based visualization system. Control tasks are handled by a Axioline-Controller from Phoenix Contact.
The start of the Ferris wheel as well as the emergency stop may not be executed by the standard control for safety reasons. Lamberink has decided to use the SafetyBridge Technology from Phoenix Contact. Safe input and output modules capture or output the signals. They also constantly perform diagnostics and monitor the module for short circuits, for example.
A logic module in the SafetyBridge installation generates and controls the safety-related transmission protocol. The protocol detects errors in the communication of the individual modules. If, for example, a transmission error occurs in an input module, the system switches to a safe state – the Ferris wheel stops. The operator is then automatically given instructions on how to rectify the fault. And if the operator does not find the fault directly, there is a mobile modem integrated into the automation solution via secure access. This means that the user on site can be supported remotely in the event of a fault. Important, because the operator is not always familiar with every technical detail of the airy pleasure.
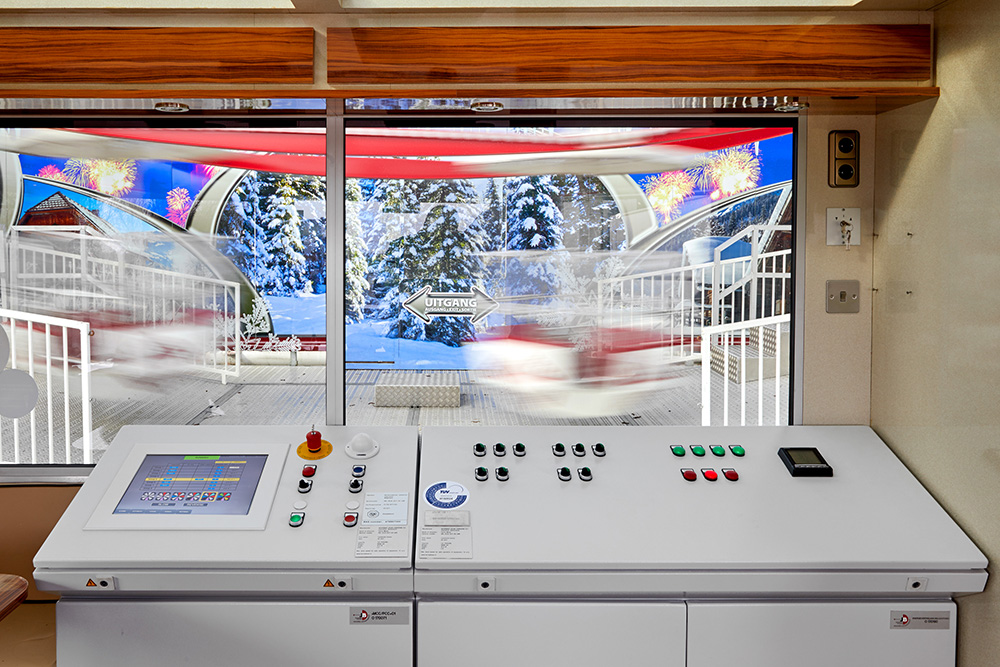
Thus secured, no height rescuer should be used in the future and no turntable ladder should provide for dizzying actions – after all, the cotton candy is certainly still waiting for the visitors on the ground.