When Reyno Thormählen looks up and sees thunderclouds, his face brightens. Thunderstorms are good. If things flash and thunder properly, his system can prove its protective function. Because Reyno Thormählen is the boss of a lightning protection company.
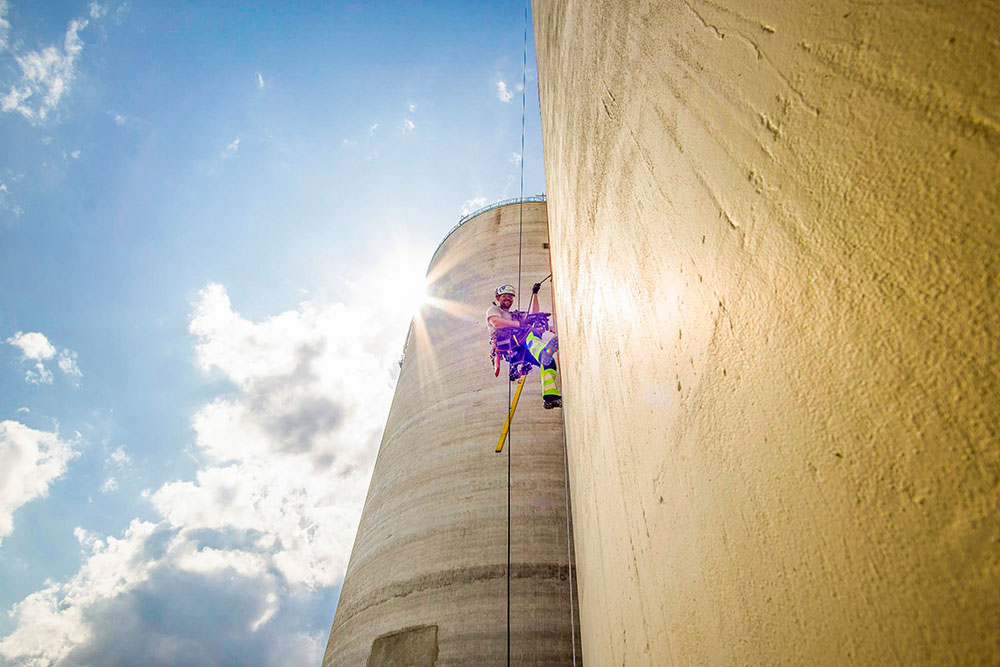
In the middle of the province of Lower Saxony, in Großenmeer near Oldenburg, you will find one of the most innovative craft enterprises in Germany. “We are the market leader in lightning protection,” Thormählen says confidently.
120 employees are working at seven locations in the north of the Federal Republic of Germany on systems that make buildings safer. “North” is a broad term in this. “We’re active as far as Cologne and Leipzig,” the general manager explains. “Approximately 80 percent of our customers come from the industrial field, ten percent from the public sector, and just as many from the private sector.”
Barracks, airports, industrial plants, wind farms – for Thormählen’s teams, things often get high up. No wonder Lower Saxony even has its own industrial climbers among its ranks. “We install lightning protection at places like North Stream 1 and 2, or are involved in the noise protection cover for the A7 motorway near Hamburg,” Thormählen says of his latest projects. The graduate e-technician is mainly responsible for strategy and marketing in the Großenmeer handicraft business.
Lazy installations
Thormählen is a model company when it comes to digitalization in the craft trades. “We are always interested in improving our procedures, streamlining processes, and avoiding the use of paper. We want to take advantage of today’s possibilities and improve our service by making our products more intelligent.”
In addition to large-scale projects, the North Germans also shine with innovations such as the under-roof lightning protection for thatched roofs (“We were the first to develop this”) and details such as using a special torque wrench to generate the tightening torque based on the material. “It’s mandatory in potentially explosive systems, but nobody has used it. It’s critical in industrial plants.”
What all lightning protection systems have in common is that most of the time, they’re doing nothing. And when they become active, nobody notices. A horror for any distributor. The only people who know how a lightning protection system works are the people who don’t have one. In other words, they find out when it’s too late. Nevertheless, the order situation is still looking good: “We have more than enough to do. The more plants are networked and IoT enters the world of production and communication, the more sensitive these fragile plants will react to the raw forces of nature,” explains Jens Barghorn, second Managing Director and, as a trained master electrician, a man of practice.
The intelligent disconnect point
Lightning units need maintenance. This is because since they are exposed to the weather, their protective function can be impaired by structural changes or they can actually become struck by lightning. In order for the technician on-site to quickly find out what the status of the system is, they must refer to the documentation available at the time. Thormählen uses special RFID identifiers from Phoenix Contact at the disconnect points for the lightning protection system, i.e. where the status is checked by taking measurements. They are housed in a weather-resistant badge, which Thormählen himself enriches with information via NFC interface and with a special industrial printer from Phoenix Contact.
“Our customer should get a talking measuring station that gives them direct information about their lightning protection system via smartphone and a suitable app,” Reyno Thormählen explains is the reason for the introduction of the “smart badges”. “We’ve conducted the real basic research together with Phoenix Contact. The first step was to test RFID chips and their antennas for their lightning compatibility. Nobody knew, for example, how the data storage on the badges would react if a lightning strike caused high-impulse currents to flow through the conductors. What material do we need to use?”
Lightning protection with vision
A separate system maintenance app has also been developed together with Phoenix Contact which allows contactless reading thanks to RFID technology. A gimmick? “Absolutely not. With this technology, facility management can integrate the system into their maintenance concept, i.e., act on their own initiative and not just follow our maintenance routine,” says Jens Barghorn, describing the advantages of disconnection point marking.
“We are currently equipping every new order with individually printed RFID badges, which currently number around 2,000 orders.” “For us, this is an investment in the relationship with our customers,” Reyno Thormählen adds. “Lightning protection is a long-term issue. We don’t want to supply just lightning protection systems, we want to offer lasting safety.”
thormaehlen.de
Industrielle Drucksysteme von Phoenix Contact