Without her strong hands and tireless dedication, today’s Phoenix Contact would not exist. Women have been the strong force behind the scenes in assembly, manufacturing, warehousing, and logistics ever since the early years of the company.
When Erika Maho and Regina Kolmsee lay their hands on the surge protection products of the Trabtech division, the two women know exactly what is important. With skilled fingers and a sharp eye, individual components are assembled to parts, inspected and remeasured, sorted out or reworked if necessary, and ultimately packaged.
After three weeks you are in
Regina Kolmsee and Erika Maho have working at Phoenix Contact for more than 30 years. They both work in the production of surge protection products at the company’s Trabtech division. Anyone visiting the ladies in Hall 9 of the multi-story production building is surrounded by women. Why have women been primarily employed in manufacturing since the company was founded? “If you want to work here, you have to have skilled fingers,” smiles Erika Maho when asked how long it would take to train a curious journalist. “And an eye for details and tricky tasks,” adds Regina Kolmsee. “But once you’ve been at it for two or three weeks, you’ve pretty much learned the skill.”
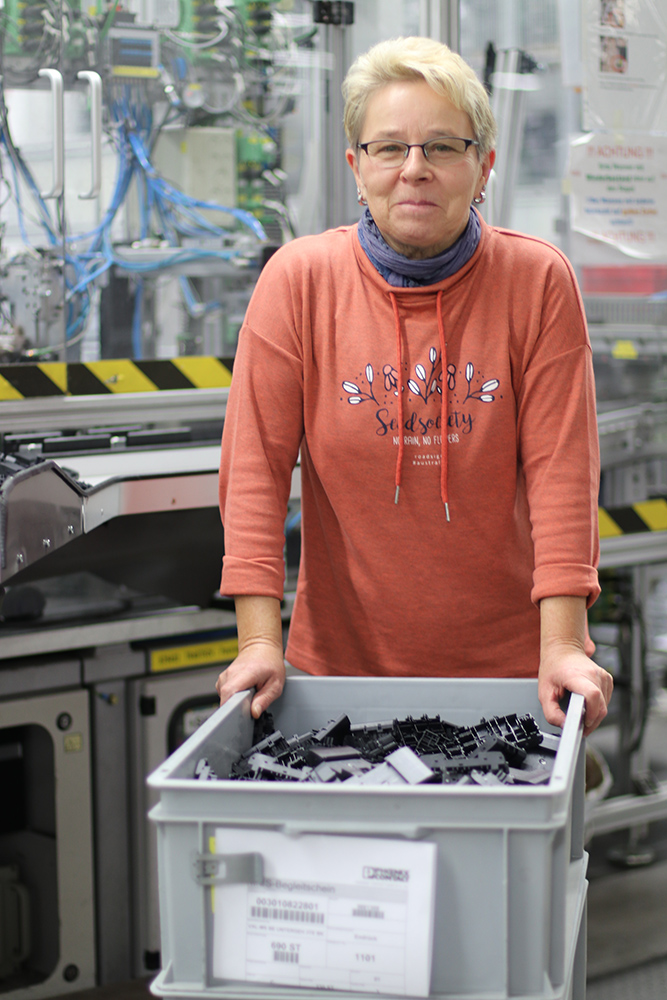
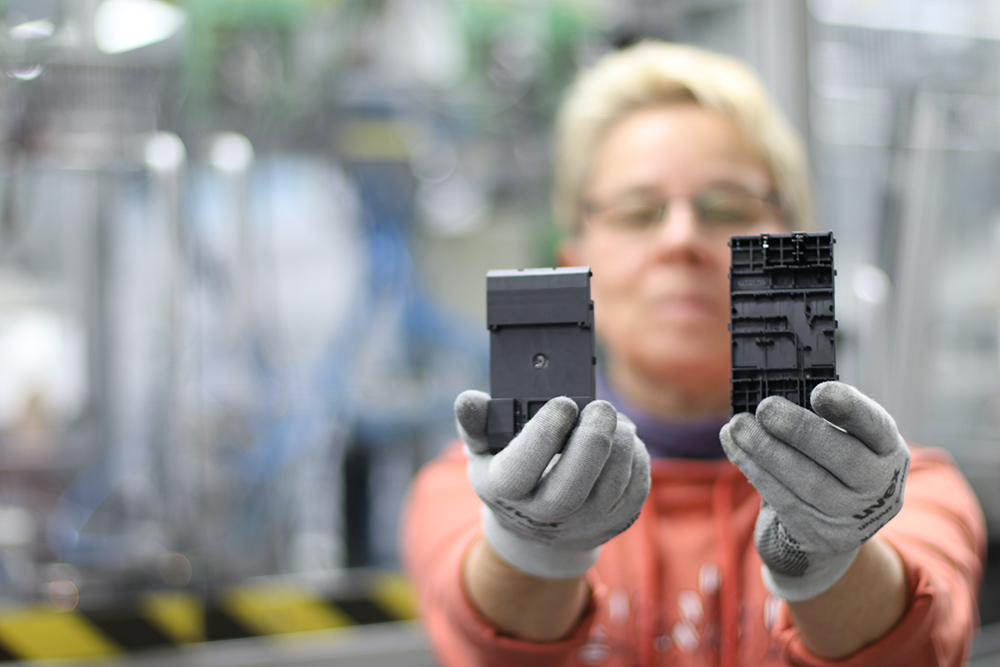
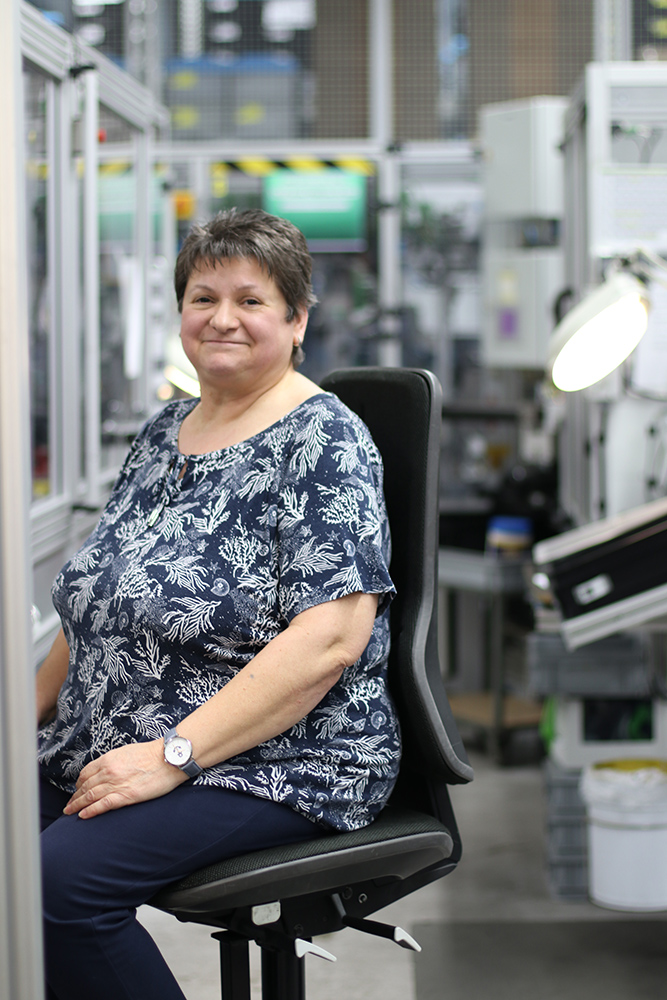
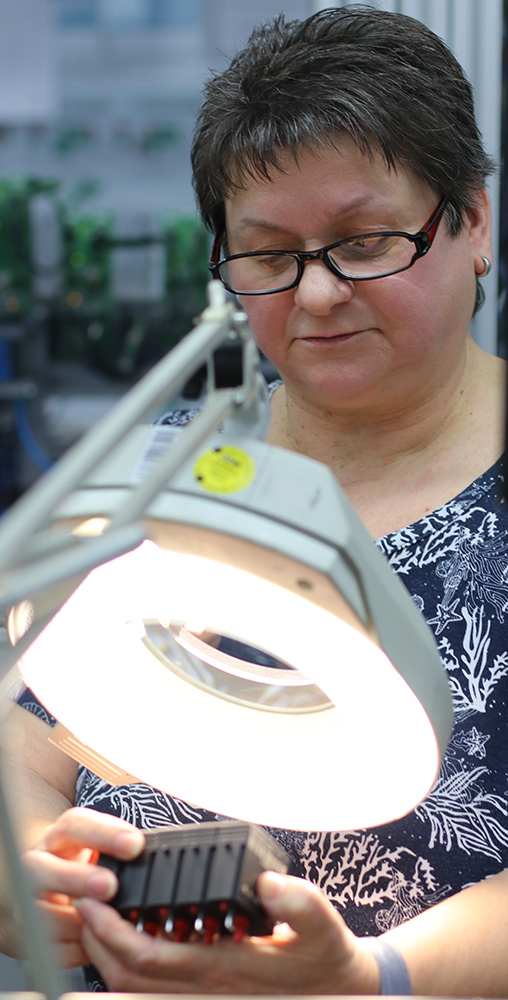
Since the start of industrialization, women have assumed an important role in value chains. Whereas until the middle of the 19th century around 75 percent of the population still lived in the countryside, this changed dramatically towards the middle to end of the 19th century. World War I further accelerated the change in the distribution of roles. In many cases, women had to assume the tasks of the men who had died in the war. Between 1907 and 1933, the number of female employees in industry and skilled trade increased by almost 500 percent.
There were also social changes as a result. In 1918, women were given the right to vote in Germany. Working woman had her own income and took on a different position in the professional world and social environment. The road to professional emancipation was still a long one, though. Until 1958 in West Germany, it was the husband who decided whether a woman was allowed to work and in what position. Until 1977, married women here still needed the husband’s consent if they wanted to work. It was not until 1980 that West Germany mandated equal pay for equal work among women and men.
Clock instead of piecework
The working environment at Phoenix Contact has seen dramatic change over the recent decades, of course. Where once this kind of work was purely manual and rather monotonous, involving the assembly of terminal blocks with simple auxiliary equipment, the workstations are now located on computer-supported production lines. Components are moved past the workstations on conveyors and await further processing. In the background, a sophisticated control system monitors to ensure the smooth flow of production. At some stations, the robotic colleague is a constant helper and sidekick.
“We rotate stations throughout the work week, depending on the incoming orders. Sometimes there are four of us at a station, assembling circuit boards, for example, and at other times we work alone on a packing unit. The work is quite diverse,” says Regina Kolmsee, describing the daily routine. After receiving training in bakery sales, she started at Phoenix Contact 36 years ago. “When I started, the percentage of manual labor we had was much higher. I started in Hall 7, where a lot of soldering tasks were still done by hand. One of my jobs that I liked to do was assembling printed circuit boards with relays, by soldering iron with feed. It was tricky, but I really enjoyed it. I like doing detail work, it’s always been my thing.”
Erika Maho has been working in manufacturing for 34 years. She adds, “Work today has become much more stressful. We used to work in piecework, too, but you could take a break here and there if you were faster. With today’s automation, that is no longer possible. The machines want to be fed continuously.”
Independent experts
The skilled workers sit in the offices at both ends of the hall. Why are there hardly any women? Erika Maho has a simple explanation: “With the household and family, women often don’t have as much time to continue their education, take advanced training courses, and then advance to become skilled workers or managers. That does happen in production, but it’s really rare.”
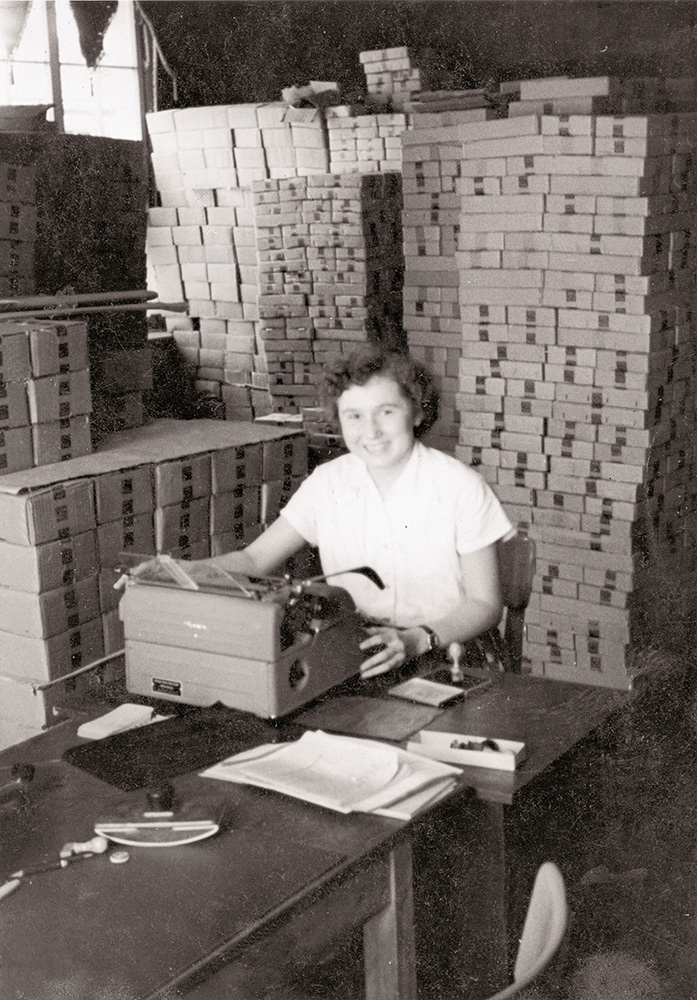
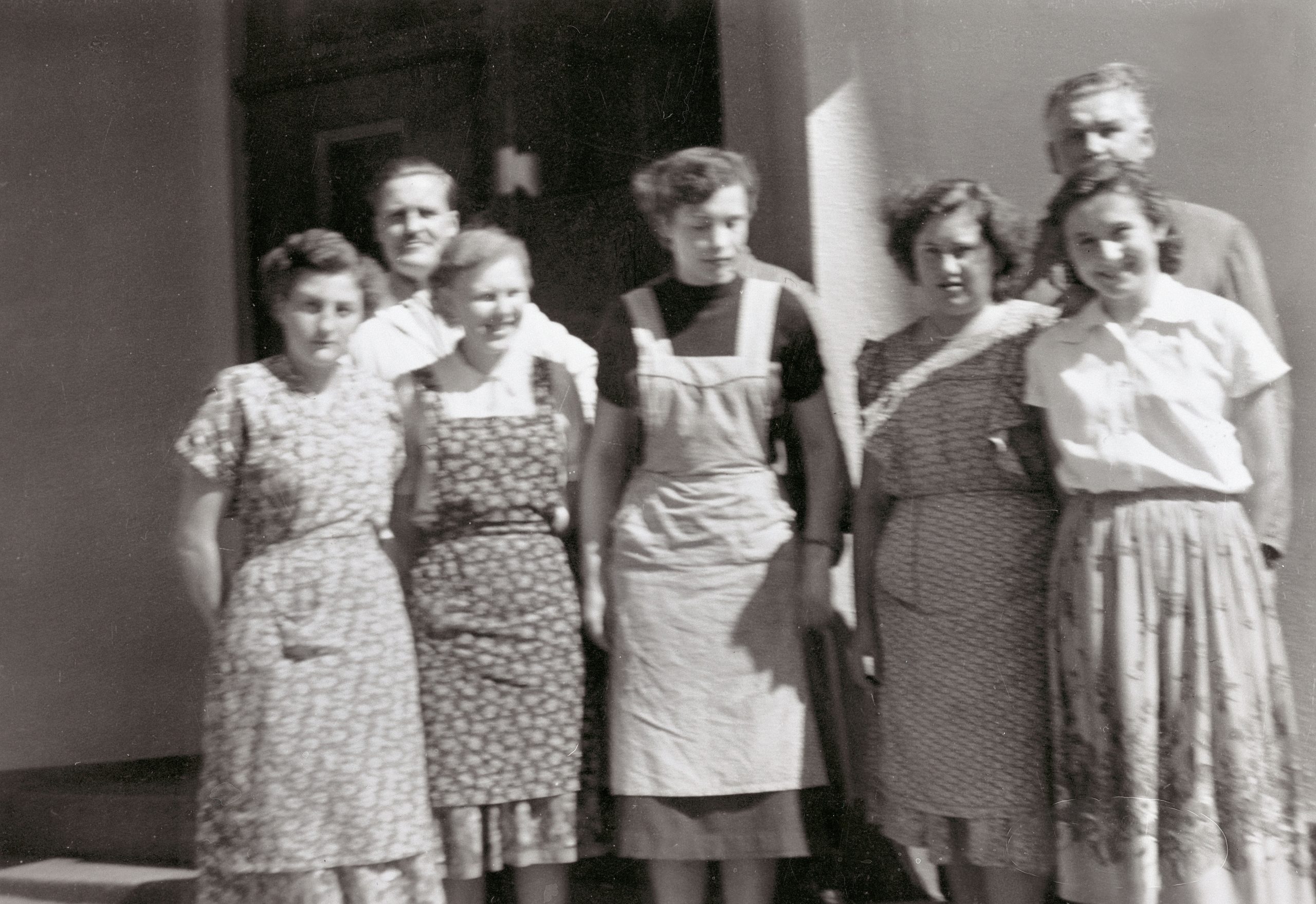
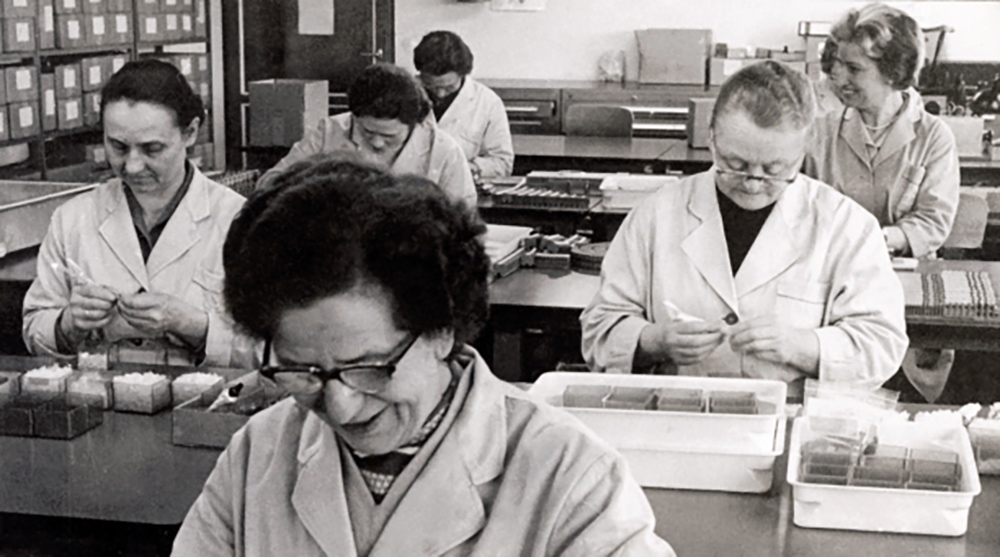
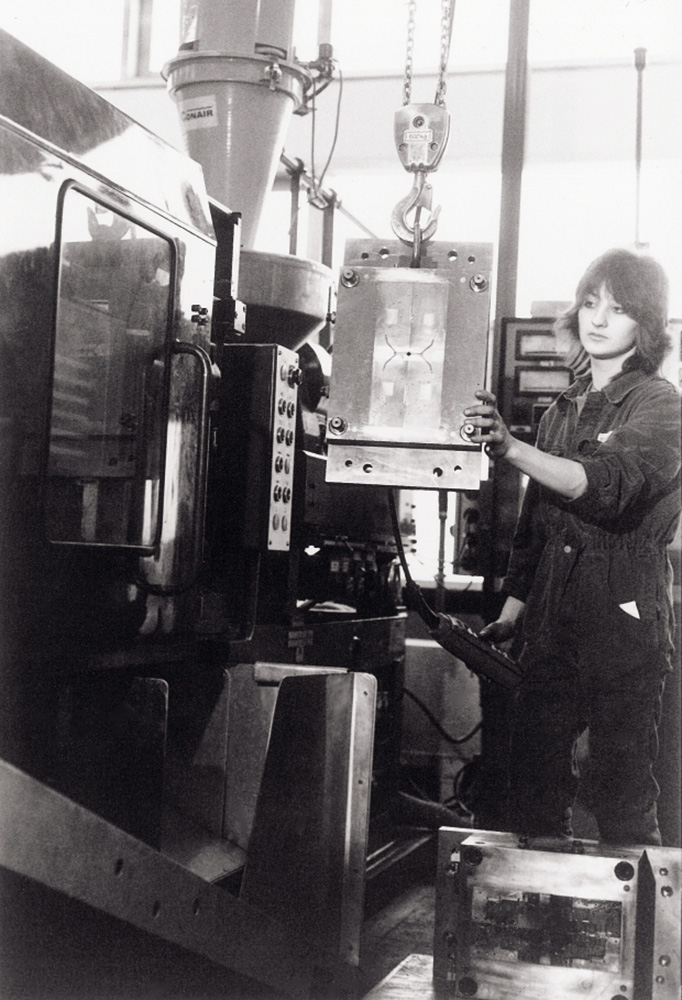
After all, it is us old hands, the ones who have been employed for a long time, who keep production going. “If one of the machines starts acting up, I first try to solve the problem myself. Most of the time I can manage, I rarely have to call in a technician for help.” Regina Kolmsee is proud of her skills. “I’m just ambitious. I want to be able to get things done myself,” Erika Maho adds: “Over the years, you get to know the ins-and-outs of your machines, so the new colleagues ask us first.”
In the arm of Klaus Eisert
It’s not just the machines, though, that are subject to the hands of time. Kolmsee and Maho represent a generation nearing retirement age. A little wistfully, they talk about the feeling of togetherness among colleagues, many of whom have already retired. And about a Phoenix Contact that was so once much smaller and more familiar when the two women started working here.
Yet, those very special Phoenix Contact moments still exist. Regina Kolmsee: “I went to see the new All Electric Society traffic circle the other day. By chance, Klaus Eisert stopped by and took some time to explain to us what was being built there. To us! His ordinary female employees. And when he was done, he put his arm on my shoulder in congratulation, pointed around at all the new buildings, and said that we had done all the work, not him. Without us and our dedication, none of this would exist. That did make me feel a little proud.”